Otto anni e l'esperienza di MECO smartANALYTICS™
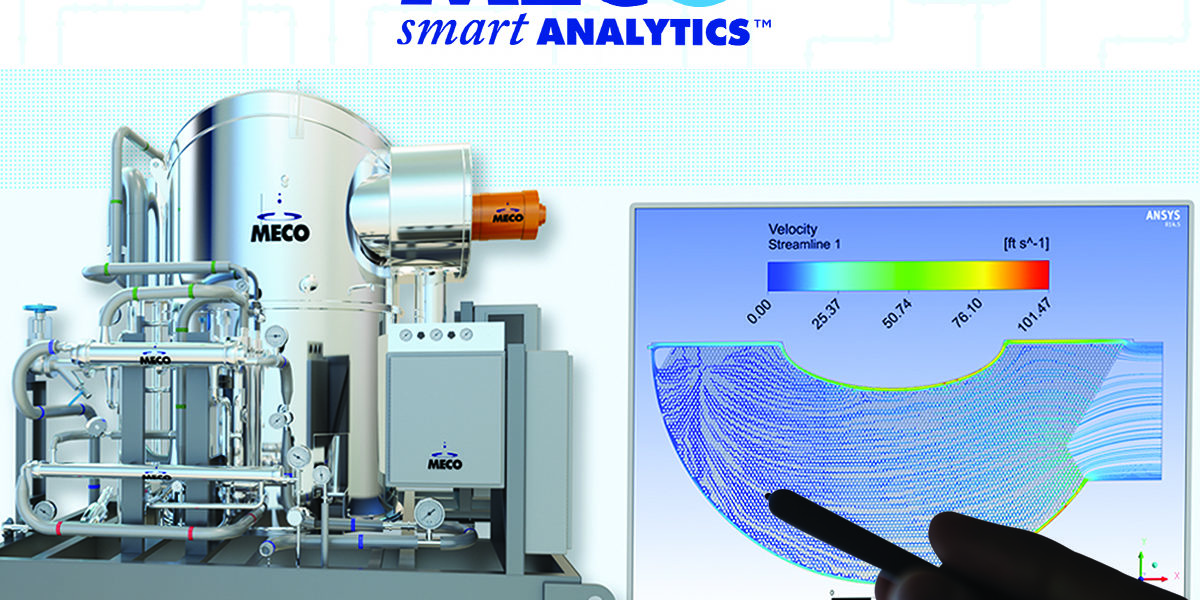
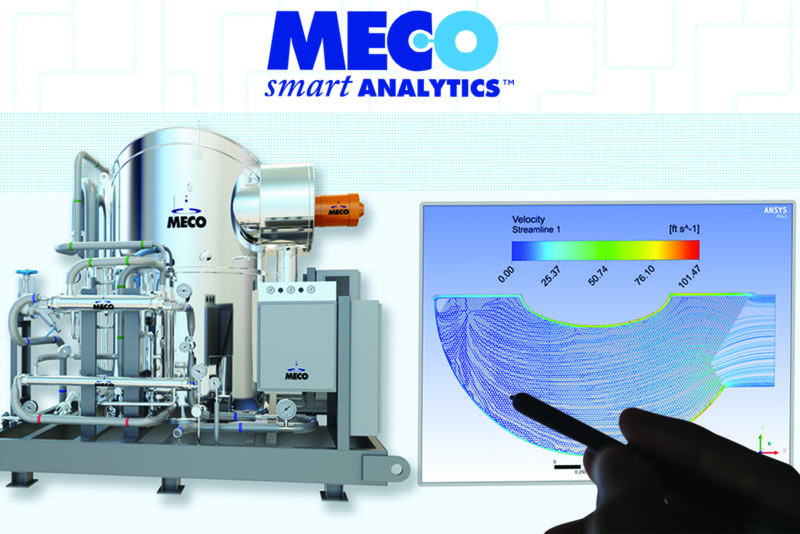
Scritto da George Gsell, presidente di MECO
Nel 2013 la Marina degli Stati Uniti, attraverso l'Office of Naval Research e il Naval Facilities Engineering Command, ha incaricato MECO di progettare e sviluppare due modelli di unità di desalinizzazione avanzate a bordo delle navi che, tra le altre cose, sarebbero state completamente autonome. La complessità e il rigore delle operazioni delle unità di desalinizzazione dell'acqua di mare richiedevano che le macchine riconoscessero i parametri di processo interni e le influenze ambientali esterne e si adattassero ai cambiamenti delle condizioni in modo che il marinaio non dovesse intervenire sulla macchina. La guida autonoma sta diventando una realtà, ma nel 2013 la tecnologia intelligente era stata a malapena introdotta nelle tecnologie più elementari, tanto meno in un processo operativo complesso come quello di un'unità di desalinizzazione a bordo di una nave.
Nel 2021, ciò che è nato dalla ricerca della Marina viene oggi definito MECO smartANALYTICS™ e incorporato nelle nostre macchine commerciali, diffuse in tutto il settore biofarmaceutico. La pandemia COVID del 2020 ha gettato una nuova luce sull'importanza e l'utilità della tecnologia analitica. La capacità di monitorare a distanza i macchinari è stata impiegata da tempo, così come le videoconferenze e le semplici telefonate. Il vantaggio di MECO smartANALYTICS™ è la capacità di avere una moltitudine di macchine sul campo, che forniscono un'ampia serie di dati, ognuna con decine di parametri di processo che si profilano rispetto a condizioni note, riconoscendo minime anomalie, affrontandole e avvisando di problemi altrimenti non rilevabili. L'obiettivo dell'analisi è quello di essere predittivi sulla manutenzione, massimizzare l'efficienza operativa, migliorare l'affidabilità del sistema e ridurre al minimo i tempi di fermo. Il monitoraggio remoto da solo non è sostenibile per quanto riguarda i suddetti obiettivi.
L'esperienza COVID
Nel 2016 MECO ha realizzato l'infrastruttura necessaria a supportare un programma di analisi commerciale diffuso. Ciò ha incluso server sicuri dedicati e la standardizzazione della strumentazione sui macchinari per fornire gli input, gli output e le comunicazioni necessarie. Il software e la programmazione sono stati sviluppati in modo tale da essere codificati all'interno del sistema e da poter essere attivati qualora il cliente decida di farlo. Alcune linee di prodotti standard, come i distillatori a compressione di vapore per la produzione di acqua per iniezione e le macchine per acqua purificata MASTERpak™, sono dotate di tecnologia e hardware.
Le restrizioni e i protocolli di sicurezza associati alla pandemia globale hanno creato oneri logistici per il servizio fisico di routine. Restrizioni di viaggio, quarantene e altri problemi si sono tradotti in ritardi e nell'impossibilità di essere fisicamente presenti quando normalmente si vorrebbe esserlo. Con l'infrastruttura già esistente, l'installazione del collegamento di comunicazione e l'attivazione dei programmi che consentono di utilizzare la tecnologia smartANALYTICS™sono operazioni relativamente semplici. La conversione avviene in pochi giorni e la diagnostica viene eseguita immediatamente dopo. Questa soluzione si è dimostrata vantaggiosa da diversi punti di vista.
In primo luogo, le visite di routine che non sarebbero state effettuate per motivi di sicurezza sono state sostituite dalla tranquillità di sapere che era stato attivato un processo analitico continuo e una serie di risorse disponibili presso il produttore, se necessario. Le visite di routine potevano essere rinviate con fiducia.
In secondo luogo, l'eliminazione della risoluzione dei problemi in loco quando si verificano. Una piacevole sorpresa è l'intimità che noi produttori abbiamo ora con un determinato sito. La nostra continua conoscenza dei parametri del sistema si traduce spesso in una più rapida risoluzione dei problemi. Le sorprese e gli interventi di emergenza si riducono notevolmente quando si ricorre all'analisi. Abbiamo una conoscenza approfondita dei macchinari e un rapporto più collaborativo con il personale del sito rispetto al passato.
Un elemento chiave di un programma analitico di successo, al di là della tecnologia impiegata, è la standardizzazione dei progetti di macchinari e sistemi. Questi standard formano una base di conoscenze e dati da cui è possibile stabilire un profilo significativo. In questo modo, il produttore ha il vantaggio di poter tracciare un profilo sulla base di dati consistenti, data la grande quantità di unità presenti sul campo. Questo è un aspetto che non è possibile con le progettazioni personalizzate una tantum o con la profilazione analitica di un singolo sito, come potrebbe fare un cliente per conto proprio.
Sicurezza
I problemi di sicurezza rappresentano il maggiore ostacolo all'implementazione di un programma di analisi. È un'altra area in cui il produttore deve investire molto per garantire la sicurezza. Ovviamente, l'hardware fisico e il routing delle comunicazioni devono essere realizzati in modo sicuro. L'architettura deve essere impostata in modo che il produttore non abbia accesso alle reti SCADA, DCS, LAN o PLC dei clienti. Oltre a questo, ci sono una serie di altre considerazioni da fare. Quali dati vengono acquisiti e sono sensibili? Sono criptati? Ci sono dispositivi di archiviazione rimovibili? È in vigore una politica sui dispositivi mobili? Qual è l'accesso e la sicurezza del personale in loco, presso il produttore o da parte di terzi? Esistono politiche documentate che vengono verificate regolarmente per verificarne la conformità? Oltre alle comunicazioni fisiche e alla gestione delle operazioni, sono importanti anche le politiche sulle risorse umane. I ruoli e le responsabilità in materia di sicurezza sono assegnati correttamente? Devono essere stipulati accordi di non divulgazione e di etica. Devono essere stabiliti processi per l'inserimento, la formazione e il cambiamento di status del personale in materia di sicurezza.
Segnalazione
La reportistica di routine e interventistica dovrebbe essere parte integrante di qualsiasi pacchetto di analisi. In questo modo, avrete la certezza di sapere che tutti i sistemi funzionano come dovrebbero o se c'è un problema che richiede la vostra attenzione. Riteniamo che il metodo di reporting top-down sia il più efficace. Sebbene vengano analizzati continuamente numerosi parametri, è possibile riassumerli rapidamente e approfondirli solo se necessario. L'affidabilità complessiva del sistema, il consumo energetico e la manutenzione in corso sono solo alcuni di questi. Anche i processi interni di reporting e comunicazione dei produttori devono essere efficienti. La necessità di assistenza dovrebbe essere proattiva, in modo da essere disponibile quando necessario. I vecchi tempi in cui ci si presentava in loco per determinare il problema, si ordinavano i pezzi, si aspettava la consegna e si tornava per risolvere il problema dovrebbero essere eliminati. Dovrebbero essere sostituiti dalla diagnostica predittiva, dalle contromisure in tempo reale e da un'adeguata programmazione.
Sintesi
Un vero programma di analisi non deve essere confuso con quello che spesso viene definito monitoraggio remoto. Prodotti ben sviluppati, abbinati agli algoritmi giusti, possono sostituire un monitoraggio reattivo meno efficace. È necessario predisporre procedure di sistema per la creazione di rapporti, la sicurezza e la manutenzione proattiva. I vantaggi per l'industria sono molteplici: il produttore di farmaci biologici, il fornitore del sistema e, in ultima analisi, il paziente. Tra questi, il risparmio di costi e di tempo, garantendo l'affidabilità e migliorando l'efficienza operativa. Le restrizioni legate alla pandemia globale hanno dato maggior valore all'implementazione di un programma di analisi. I problemi di sicurezza possono essere affrontati in modo specifico con l'infrastruttura e le politiche adeguate.