Oito anos depois e a experiência da MECO smartANALYTICS™
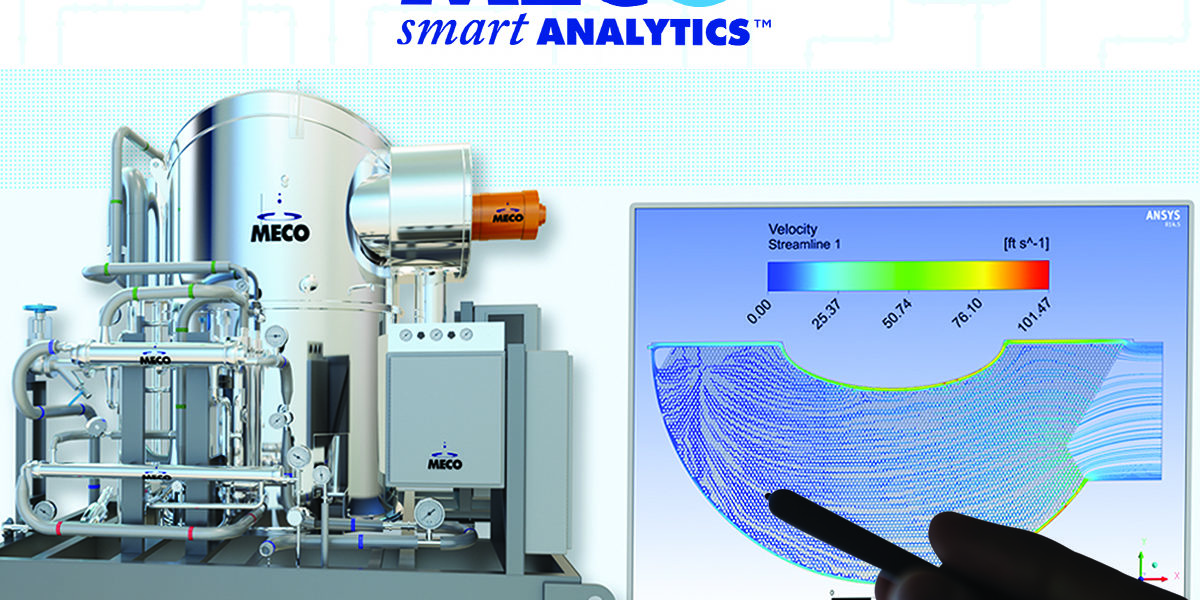
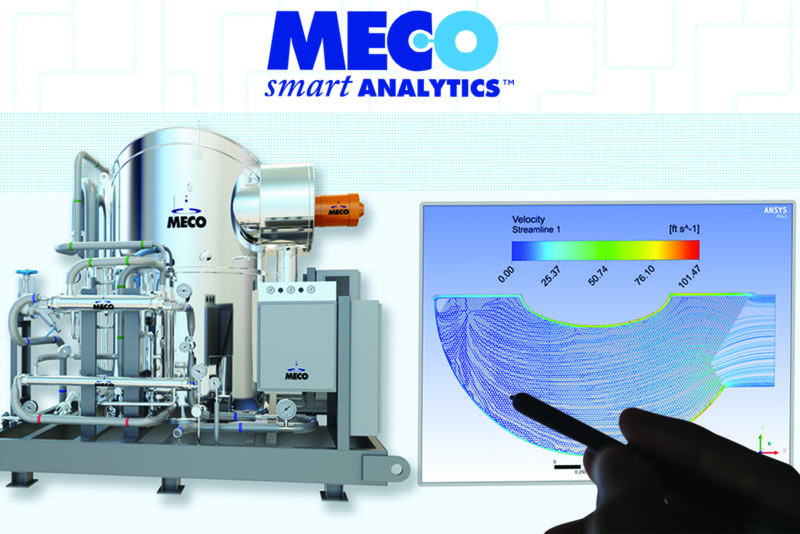
Escrito por George Gsell, Presidente da MECO
Em 2013, a Marinha dos EUA, através do Office of Naval Research e do Naval Facilities Engineering Command, contratou a MECO para conceber e desenvolver dois modelos de unidades avançadas de dessalinização a bordo que, entre outras coisas, seriam completamente autónomas. A complexidade e o rigor das operações das unidades de dessalinização de água do mar significavam que as máquinas teriam de reconhecer os parâmetros internos do processo, bem como as influências ambientais externas, e adaptar-se às condições em mudança, de modo a que o marinheiro não tivesse qualquer intervenção na máquina. A condução autónoma está agora a tornar-se uma realidade, mas em 2013, a tecnologia inteligente ainda mal tinha sido introduzida nas tecnologias mais básicas, muito menos numa operação de processo tão complexa como uma unidade de dessalinização a bordo de um navio.
Avançando para 2021, hoje o que nasceu da investigação da Marinha é denominado MECO smartANALYTICS™ e está incorporado nas nossas máquinas comerciais predominantes em toda a indústria biofarmacêutica. A pandemia de COVID de 2020 lançou uma nova luz sobre a importância e a utilidade da tecnologia analítica. A capacidade de monitorizar remotamente as máquinas é utilizada há muito tempo, tal como a videoconferência e uma simples chamada telefónica. A vantagem do MECO smartANALYTICS™ é a sua capacidade de ter uma multiplicidade de máquinas no terreno, fornecendo um grande conjunto de dados, cada uma com dezenas de parâmetros de processo que se perfilam em relação a condições conhecidas, reconhecendo anomalias minúsculas, lidando com essas anomalias e alertando para problemas que de outra forma seriam indetetáveis. O objetivo da análise é ser preditivo na manutenção, maximizar a eficiência operacional, melhorar a fiabilidade do sistema e minimizar o tempo de inatividade. A monitorização remota, por si só, não é sustentável no que diz respeito aos objectivos acima referidos.
A experiência COVID
A MECO construiu a infraestrutura necessária para suportar um programa de análise comercial generalizado em 2016. Isso incluiu servidores seguros dedicados e a padronização da instrumentação em máquinas para fornecer as entradas, saídas e comunicação necessárias. O software e a programação foram desenvolvidos de forma a estarem codificados no sistema e poderem ser activados se o cliente assim o desejar. Determinadas linhas de produtos padrão, como os destiladores de compressão de vapor para a produção de água para injeção e as máquinas MASTERpak™Purified Water, têm a tecnologia e o hardware instalados.
As restrições e os protocolos de segurança associados à pandemia global criaram encargos logísticos para o serviço físico de rotina. As restrições de viagem, as quarentenas e outras questões traduziram-se em atrasos e na impossibilidade de estar fisicamente presente quando normalmente se desejaria estar. Com a infraestrutura já instalada, é uma conversão relativamente simples instalar a ligação de comunicação e ativar os programas de modo a que a tecnologia smartANALYTICS™possa ser utilizada. A conversão ocorre numa questão de dias e o diagnóstico é efectuado imediatamente a seguir. Isto provou ser benéfico de vários pontos de vista.
Em primeiro lugar, as visitas de rotina que não se realizavam por razões de segurança foram substituídas pela tranquilidade de saber que havia um processo de análise em curso ativado e uma série de recursos disponíveis no fabricante, se necessário. Essas visitas de rotina podiam ser adiadas com confiança.
Em segundo lugar, a eliminação da resolução de problemas no local quando surgem problemas. Uma agradável surpresa é a intimidade que nós, como fabricantes, temos agora com um determinado local. O nosso conhecimento contínuo dos parâmetros do sistema traduz-se frequentemente numa resolução mais rápida dos problemas. As surpresas e o serviço de emergência são largamente reduzidos quando a análise é efectuada. Temos conhecimentos profundos sobre a maquinaria e uma relação de colaboração com o pessoal do estaleiro mais do que nunca.
Um elemento-chave de um programa analítico bem sucedido, para além da tecnologia utilizada, é a normalização das concepções de máquinas e sistemas. Esses padrões formam uma base de conhecimento e dados a partir da qual é possível estabelecer um perfil significativo. Como tal, o fabricante tem a vantagem de criar perfis com base em dados substanciais, dada a maior população de unidades no terreno. Isto é algo que não é possível com projectos personalizados únicos ou com a definição de perfis analíticos de um único local, como um cliente pode fazer por si próprio.
Segurança
As preocupações com a segurança representam o maior obstáculo à implementação de um programa de análise. É outra área em que o fabricante tem de investir fortemente para garantir a segurança. Obviamente, o hardware físico e o encaminhamento das comunicações têm de ser efectuados de forma segura. A arquitetura deve ser configurada de modo a que o fabricante não tenha acesso às redes SCADA, DCS, LAN ou PLC dos clientes. Para além disso, há uma série de outras considerações que devem ser tidas em conta. Que dados estão a ser adquiridos e são sensíveis? Estão encriptados? Existem dispositivos de armazenamento amovíveis? Existe uma política de dispositivos móveis em vigor? Qual é o acesso e a segurança do pessoal no local, no fabricante ou por terceiros? Existem políticas documentadas que são objeto de auditorias de rotina para verificar a sua conformidade? Para além das comunicações físicas e da gestão de operações adequadas, as políticas de recursos humanos também são importantes. As funções e responsabilidades pela segurança estão corretamente atribuídas? Devem estar em vigor acordos de não divulgação e de ética. Devem existir processos estabelecidos para a integração do pessoal, formação e mudança de estatuto relativamente à segurança.
Relatórios
Os relatórios de rotina e de intervenção devem fazer parte de qualquer pacote analítico. Desta forma, terá a confiança necessária para saber se todos os sistemas estão a funcionar como devem ou se existe algum problema que necessite da sua atenção. Consideramos que o método de elaboração de relatórios de cima para baixo é o mais eficaz. Apesar de estarem continuamente a ser analisados vários parâmetros, estes podem ser resumidos rapidamente e aprofundados apenas se necessário. A fiabilidade geral do sistema, o consumo de energia e a manutenção pendente são apenas alguns deles. Os processos internos de comunicação e de elaboração de relatórios do fabricante também devem ser eficientes. A necessidade de assistência técnica deve ser proactiva, de modo a estar disponível quando necessário. Os velhos tempos de comparência no local para determinar o problema, encomendar peças, aguardar a entrega e regressar para resolver o problema devem ser eliminados. Devem ser substituídos por diagnósticos preditivos, contramedidas em tempo real e uma programação adequada.
Resumo
Um verdadeiro programa de análise não deve ser confundido com o que é frequentemente designado por monitorização remota. Produtos bem desenvolvidos, associados aos algoritmos certos, podem substituir uma monitorização reactiva menos eficaz. Devem existir procedimentos de sistema para a elaboração de relatórios, segurança e manutenção proactiva. Há vantagens para a indústria, incluindo o fabricante de produtos biológicos, o fornecedor do sistema e, em última análise, o doente. Estas incluem poupanças de custos e de tempo, assegurando simultaneamente a fiabilidade e melhorando a eficiência operacional. As restrições relacionadas com a pandemia global valorizaram ainda mais a implementação de um programa de análise. As preocupações com a segurança podem ser especificamente abordadas com a infraestrutura e as políticas adequadas em vigor.