Eight Years On and the Experience of MECO smartANALYTICS™
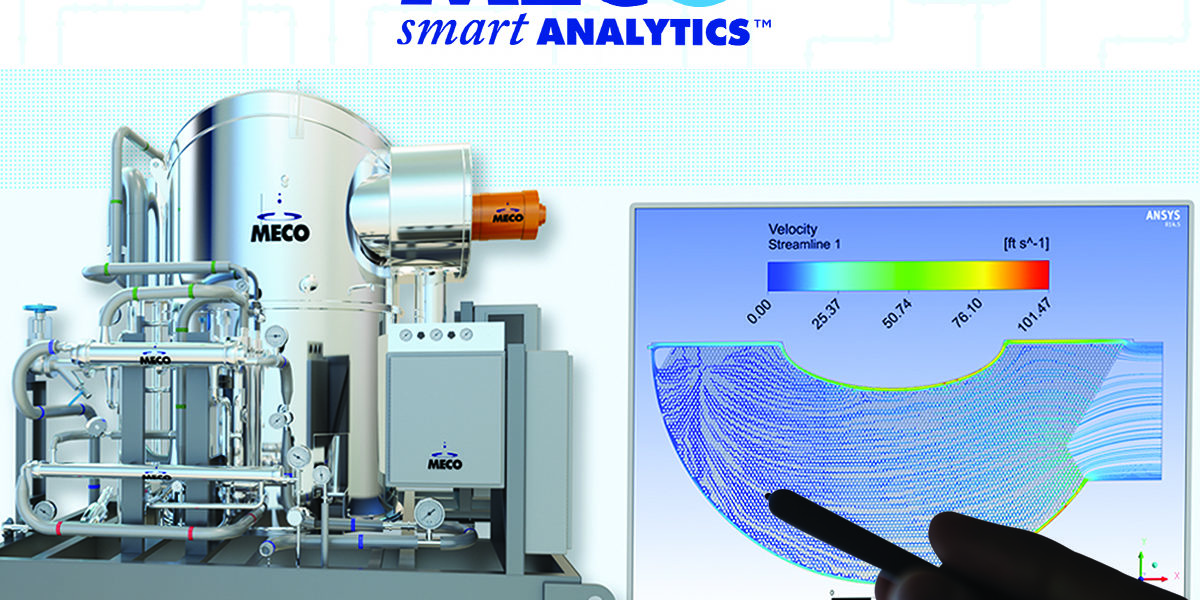
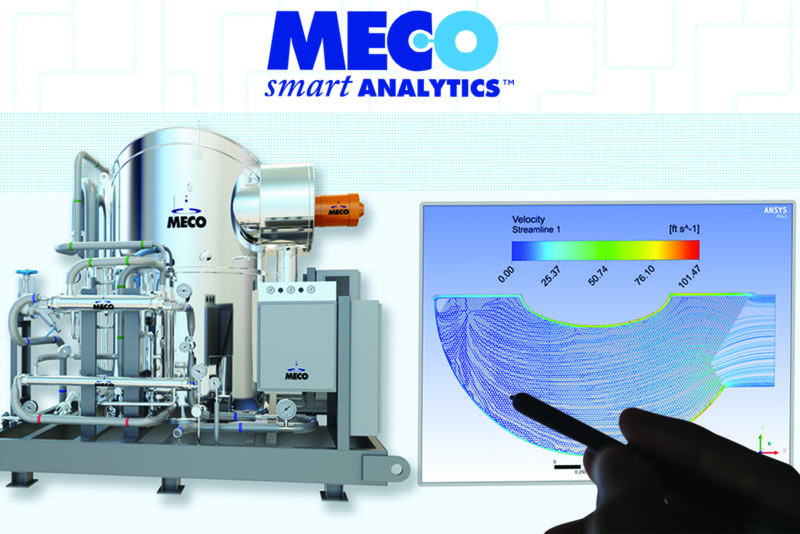
Written by George Gsell, MECO’s President
In 2013 the US Navy through the Office of Naval Research and Naval Facilities Engineering Command contracted MECO to design and develop two models of advanced shipboard desalination units that, among other things, would be completely autonomous. The complexity and rigors of seawater desalination unit operations meant that the machines would have to recognize internal process parameters as well as outside environmental influences and adapt to changing conditions such that the sailor had no intervention with the machine. Autonomous driving is now becoming a reality but in 2013, smart technology had barely been introduced into the most basic technologies, much less a process operation as complex as a shipboard desalination unit.
Fast forward to 2021 and today what was borne out of the Navy research is termed MECO smartANALYTICS™ and imbedded within our commercial machines prevalent throughout the biopharmaceutical industry. The COVID pandemic of 2020 shed a new light on the importance and usefulness of analytics technology. The ability to remotely monitor machinery has long been employed as has video conferencing and a simple phone call. The advantage of MECO smartANALYTICS™ is its capability to have a multitude of machines in the field, providing a large set of data, each with dozens of process parameters profiling themselves against known conditions, recognizing minute anomalies, dealing with those anomalies, and alerting to otherwise undetectable issues. The objective of analytics is to be predictive on maintenance, maximize operational efficiency, improve system reliability, and minimize downtime. Remote monitoring alone is simply not sustainable with respect to the foregoing objectives.
The COVID Experience
MECO built the infrastructure necessary to support a widespread commercial analytics program in 2016. This included dedicated secure servers and the standardizing of instrumentation on machinery to provide the necessary inputs, outputs, and communication. Software and programming were developed such that it is coded within the system and can be activated should the client choose to do so. Certain standard product lines such as vapor compression distillers for the production of Water for Injection and MASTERpak™ Purified Water machines have the technology and hardware installed.
The restrictions and safety protocols associated with the global pandemic created logistical burdens on routine physical service. Travel restrictions, quarantines and other issues translated to delays and the inability to be physically present when one would normally want to be. With the infrastructure already in place, it is a relatively simple conversion to install the communication link and activate the programs such that the smartANALYTICS™ technology can be engaged. The conversion takes place in a matter of days and diagnostics run immediately thereafter. This has proved beneficial from a number of standpoints.
First, routine visits which were not going to take place for safety reasons were replaced with the peace of mind that there was an ongoing analytics process activated and a host of resources available at the manufacturer if necessary. Those routine visits could be deferred with confidence.
Second was the elimination of onsite troubleshooting when issues do arise. One pleasant surprise is the intimacy that we as manufacturers now have with a given site. Our ongoing knowledge of system parameters often translates to more rapid resolution of issues. Surprises and emergency service is largely reduced when analytics are engaged. We have in-depth insights into the machinery and more collaborative relationship with site personnel than ever before.
A key element of a successful analytics program beyond the technology employed is the standardization of machinery and system designs. Those standards form a baseline of knowledge and data from which meaningful profiling can be established. As such, the manufacturer has the benefit of profiling against substantial data given the larger population of units in the field. This is something which is not possible with one off custom designs or analytical profiling of a single site such as a client might do on their own.
Security
Security concerns represent the biggest hurdle to implementing an analytics program. It is another area where the manufacturer has to be heavily invested in order to ensure safety. Obviously, the physical hardware and communication routing needs to be done in a secure manner. The architecture should be set up such that the manufacturer does not have access to the clients SCADA, DCS, LAN or PLC networks. Beyond that, there are a host of other considerations that should be addressed. What data is being acquired and is it sensitive? Is it encrypted? Are there removable storage devices? Is there a mobile device policy in place? What personnel access and security is there onsite, at the manufacturer or by third parties? Are there documented policies that are audited routinely for compliance? In addition to the proper physical communications and operations management, human resource policies are also important. Are roles and responsibilities for security properly allocated? Agreements for non-disclosure and ethics should be in place. Established processes for personnel onboarding, training and change of status relative to security should be in place.
Reporting
Routine and interventional reporting should be a part of any analytics package. In this way, you will have the confidence to know that all systems are working as they should or if there is an issue that needs your attention. We find a top-down reporting method to be most effective. Although numerous parameters are continuously being analyzed, they can be summarized quickly and drilled down on only if necessary. System overall reliability, energy consumption and pending maintenance are just a few. The manufacturers internal reporting and communication processes should be efficient as well. The need for service should be proactive such that they are available when needed. The old days of showing up onsite to determine what the problem is, ordering parts, waiting on delivery, and returning to fix an issue should be eliminated. They should be replaced through predictive diagnostics, real time countermeasures and proper scheduling.
Summary
A true analytics program should not be confused with what is often termed as remote monitoring. Well developed products coupled with the right algorithms can replace less effective reactive monitoring. System procedures for reporting, security and proactive maintenance should be in place. There are benefits to the industry including the biologics manufacturer, the system supplier and ultimately the patient. These include savings in cost and time while assuring reliability and improving operational efficiency. The restrictions related to the global pandemic have put an increased value on the implementation of an analytics program. Security concerns can be specifically addressed with the proper infrastructure and policies in place.