Acht Jahre und die Erfahrung von MECO smartANALYTICS™
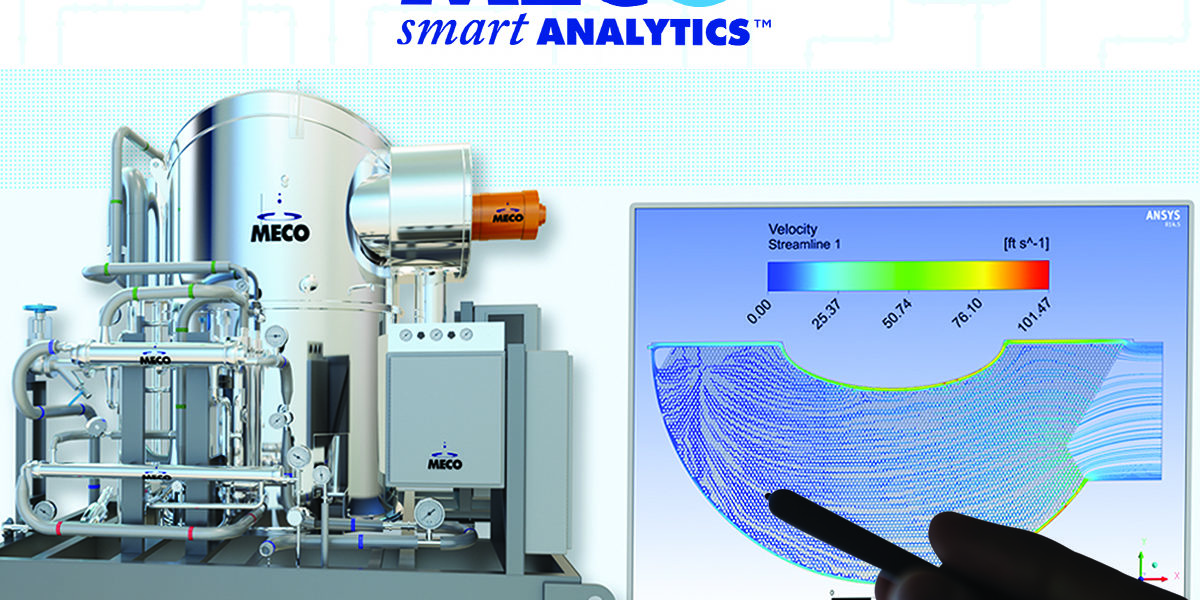
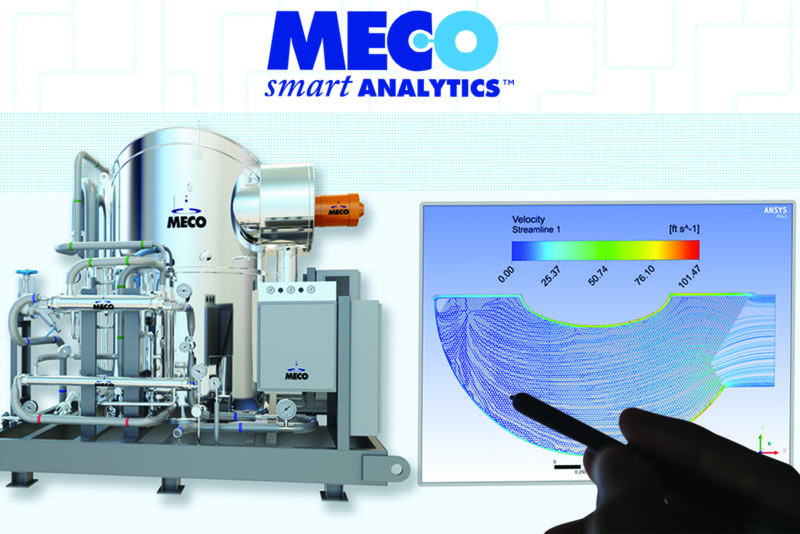
Geschrieben von George Gsell, MECOs Präsident
2013 beauftragte die US-Marine über das Office of Naval Research und das Naval Facilities Engineering Command MECO mit dem Entwurf und der Entwicklung von zwei Modellen fortschrittlicher Entsalzungsanlagen an Bord von Schiffen, die u. a. völlig autonom arbeiten sollten. Aufgrund der Komplexität und Härte des Betriebs von Meerwasserentsalzungsanlagen mussten die Maschinen sowohl interne Prozessparameter als auch äußere Umwelteinflüsse erkennen und sich an veränderte Bedingungen anpassen, so dass der Matrose keinen Einfluss auf die Maschine nehmen musste. Das autonome Fahren ist inzwischen Realität, aber 2013 war die intelligente Technologie kaum in die grundlegendsten Technologien eingeführt worden, geschweige denn in einen so komplexen Prozess wie eine Entsalzungsanlage an Bord eines Schiffes.
Spulen Sie bis 2021 vor, und heute wird das, was aus der Marineforschung hervorging, als MECO smartANALYTICS™ bezeichnet und in unsere kommerziellen Maschinen integriert, die in der biopharmazeutischen Industrie weit verbreitet sind. Die COVID-Pandemie von 2020 warf ein neues Licht auf die Bedeutung und den Nutzen der Analysetechnologie. Die Möglichkeit, Maschinen aus der Ferne zu überwachen, wird seit langem genutzt, ebenso wie Videokonferenzen oder ein einfacher Telefonanruf. Der Vorteil von MECO smartANALYTICS™ ist die Fähigkeit, eine Vielzahl von Maschinen im Feld zu haben, die einen großen Datensatz liefern, jede mit Dutzenden von Prozessparametern, die sich selbst mit bekannten Bedingungen vergleichen, winzige Anomalien erkennen, mit diesen Anomalien umgehen und bei ansonsten unerkennbaren Problemen Alarm schlagen. Ziel der Analytik ist es, die Wartung vorausschauend zu gestalten, die betriebliche Effizienz zu maximieren, die Systemzuverlässigkeit zu verbessern und Ausfallzeiten zu minimieren. Fernüberwachung allein ist im Hinblick auf die vorgenannten Ziele einfach nicht nachhaltig.
Die COVID-Erfahrung
MECO baute die Infrastruktur auf, die zur Unterstützung eines weit verbreiteten kommerziellen Analyseprogramms im Jahr 2016 erforderlich war. Dazu gehörten dedizierte sichere Server und die Standardisierung der Instrumentierung von Maschinen, um die erforderlichen Eingaben, Ausgaben und die Kommunikation zu ermöglichen. Software und Programmierung wurden so entwickelt, dass sie im System kodiert sind und auf Wunsch des Kunden aktiviert werden können. Bestimmte Standardproduktlinien wie Dampfkompressionsdestillatoren für die Herstellung von Wasser für Injektionszwecke und MASTERpak™-Maschinenfür gereinigtes Wasser sind mit der entsprechenden Technologie und Hardware ausgestattet.
Die Beschränkungen und Sicherheitsprotokolle im Zusammenhang mit der weltweiten Pandemie führten zu logistischen Belastungen für den routinemäßigen physischen Dienst. Reisebeschränkungen, Quarantänen und andere Probleme führten zu Verspätungen und der Unmöglichkeit, physisch anwesend zu sein, wenn man es eigentlich wollte. Da die Infrastruktur bereits vorhanden ist, ist es eine relativ einfache Umstellung, die Kommunikationsverbindung zu installieren und die Programme zu aktivieren, so dass die smartANALYTICS™-Technologieeingesetzt werden kann. Die Umstellung erfolgt innerhalb weniger Tage, und die Diagnose läuft unmittelbar danach. Dies hat sich unter mehreren Gesichtspunkten als vorteilhaft erwiesen.
Erstens wurden Routinebesuche, die aus Sicherheitsgründen nicht stattfinden sollten, durch die Gewissheit ersetzt, dass ein laufender Analyseprozess aktiviert war und der Hersteller bei Bedarf über eine Vielzahl von Ressourcen verfügte. Diese Routinebesuche konnten getrost verschoben werden.
Zweitens entfällt die Fehlersuche vor Ort, wenn Probleme auftauchen. Eine angenehme Überraschung ist die Vertrautheit, die wir als Hersteller jetzt mit einem bestimmten Standort haben. Unsere ständige Kenntnis der Systemparameter führt oft zu einer schnelleren Lösung von Problemen. Überraschungen und Notdiensteinsätze werden durch den Einsatz der Analytik weitgehend reduziert. Wir haben einen tieferen Einblick in die Maschinen und arbeiten enger mit dem Personal vor Ort zusammen als je zuvor.
Ein Schlüsselelement eines erfolgreichen Analyseprogramms, das über die eingesetzte Technologie hinausgeht, ist die Standardisierung von Maschinen- und Systemkonzepten. Diese Standards bilden eine Wissens- und Datenbasis, auf deren Grundlage eine aussagekräftige Profilierung vorgenommen werden kann. So hat der Hersteller den Vorteil, dass er auf der Grundlage einer größeren Anzahl von Einheiten im Feld ein Profil erstellen kann. Dies ist etwas, was bei kundenspezifischen Einzelanfertigungen oder analytischen Profilerstellungen an einem einzelnen Standort, wie sie ein Kunde auf eigene Faust durchführen könnte, nicht möglich ist.
Sicherheit
Sicherheitsbedenken stellen die größte Hürde bei der Einführung eines Analyseprogramms dar. Dies ist ein weiterer Bereich, in den der Hersteller stark investieren muss, um die Sicherheit zu gewährleisten. Es liegt auf der Hand, dass die physische Hardware und das Kommunikationsrouting auf sichere Weise erfolgen müssen. Die Architektur sollte so eingerichtet werden, dass der Hersteller keinen Zugang zu den SCADA-, DCS-, LAN- oder SPS-Netzen der Kunden hat. Darüber hinaus gibt es eine ganze Reihe weiterer Überlegungen, die berücksichtigt werden sollten. Welche Daten werden erfasst und sind sie sensibel? Sind sie verschlüsselt? Gibt es Wechselspeichergeräte? Gibt es eine Richtlinie für mobile Geräte? Welchen Zugang und welche Sicherheit hat das Personal vor Ort, beim Hersteller oder durch Dritte? Gibt es dokumentierte Richtlinien, die routinemäßig auf ihre Einhaltung überprüft werden? Neben der ordnungsgemäßen physischen Kommunikation und dem Betriebsmanagement sind auch die Personalrichtlinien von Bedeutung. Sind die Rollen und Verantwortlichkeiten für die Sicherheit richtig verteilt? Es sollten Vertraulichkeits- und Ethikvereinbarungen vorhanden sein. Es sollten etablierte Verfahren für die Einarbeitung, Schulung und Statusänderung des Personals in Bezug auf die Sicherheit vorhanden sein.
Berichterstattung
Routine- und Interventionsberichte sollten Teil eines jeden Analysepakets sein. Auf diese Weise haben Sie die Gewissheit, dass alle Systeme ordnungsgemäß funktionieren oder dass es ein Problem gibt, das Ihre Aufmerksamkeit erfordert. Unserer Meinung nach ist eine Top-down-Berichtsmethode am effektivsten. Obwohl ständig zahlreiche Parameter analysiert werden, lassen sie sich schnell zusammenfassen und nur bei Bedarf detailliert aufschlüsseln. Die Gesamtzuverlässigkeit des Systems, der Energieverbrauch und anstehende Wartungsarbeiten sind nur einige davon. Auch die internen Berichts- und Kommunikationsprozesse des Herstellers sollten effizient sein. Der Bedarf an Serviceleistungen sollte proaktiv sein, damit sie bei Bedarf zur Verfügung stehen. Die alten Zeiten, in denen man vor Ort auftauchte, um das Problem festzustellen, Teile bestellte, auf die Lieferung wartete und zurückkehrte, um ein Problem zu beheben, sollten der Vergangenheit angehören. Sie sollten durch prädiktive Diagnostik, Gegenmaßnahmen in Echtzeit und eine angemessene Zeitplanung ersetzt werden.
Zusammenfassung
Ein echtes Analyseprogramm sollte nicht mit dem verwechselt werden, was oft als Fernüberwachung bezeichnet wird. Gut entwickelte Produkte in Verbindung mit den richtigen Algorithmen können eine weniger effektive reaktive Überwachung ersetzen. Es sollten Systemverfahren für die Berichterstattung, Sicherheit und proaktive Wartung vorhanden sein. Die Vorteile für die Industrie, einschließlich des Biologika-Herstellers, des Systemanbieters und letztlich des Patienten, liegen auf der Hand. Dazu gehören Kosten- und Zeiteinsparungen bei gleichzeitiger Gewährleistung der Zuverlässigkeit und Verbesserung der betrieblichen Effizienz. Die Einschränkungen im Zusammenhang mit der weltweiten Pandemie haben der Implementierung eines Analyseprogramms einen höheren Stellenwert verliehen. Sicherheitsbedenken können mit der richtigen Infrastruktur und den entsprechenden Richtlinien gezielt angegangen werden.