Ocho años después y la experiencia de MECO smartANALYTICS™.
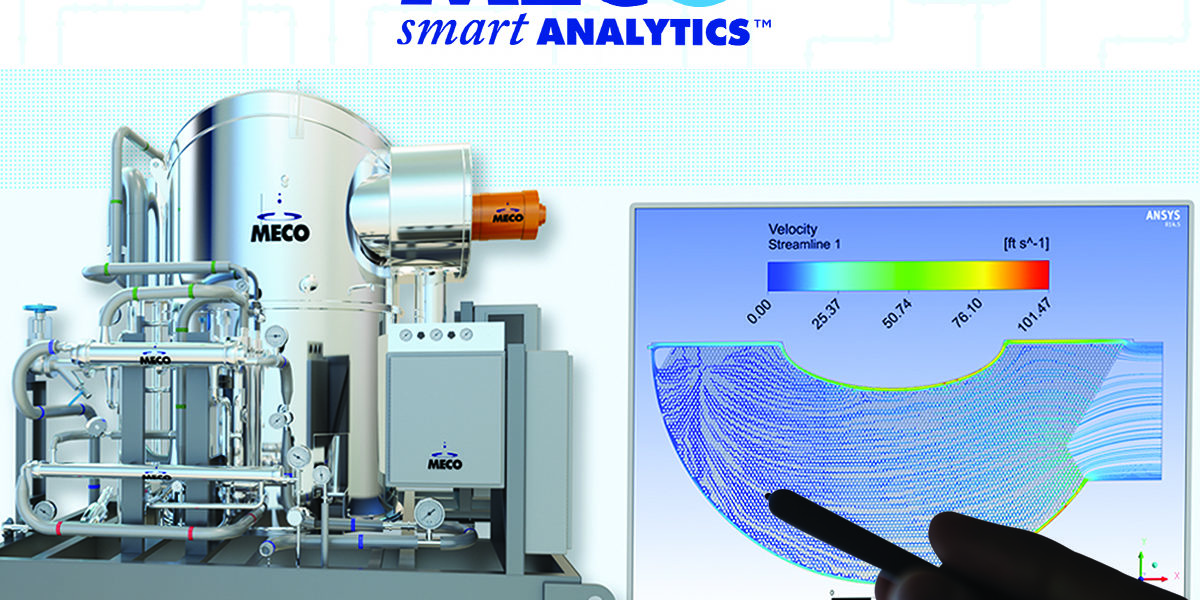
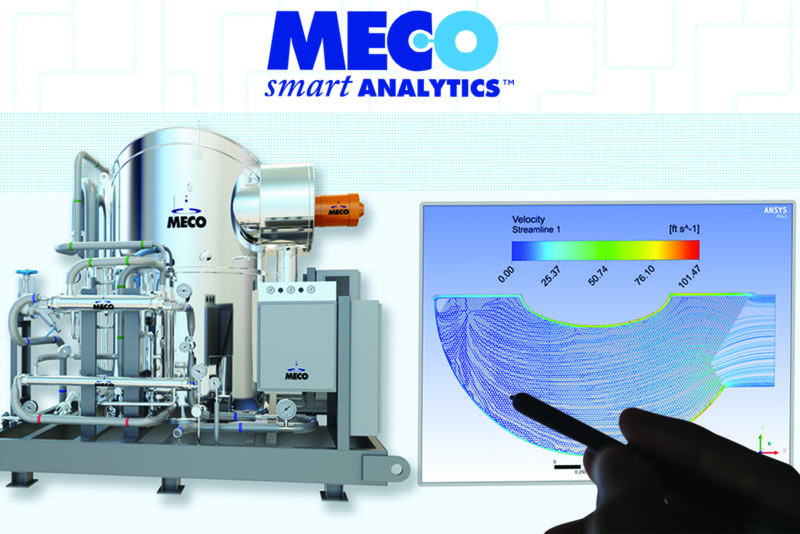
Escrito por George Gsell, Presidente de MECO
En 2013, la Marina estadounidense, a través de la Oficina de Investigación Naval y el Mando de Ingeniería de Instalaciones Navales, contrató a MECO para diseñar y desarrollar dos modelos de unidades avanzadas de desalinización a bordo que, entre otras cosas, fueran completamente autónomas. La complejidad y el rigor de las operaciones de las unidades de desalinización de agua de mar implicaban que las máquinas tendrían que reconocer los parámetros internos del proceso, así como las influencias ambientales externas, y adaptarse a las condiciones cambiantes de forma que el marinero no tuviera que intervenir en la máquina. La conducción autónoma se está convirtiendo en una realidad, pero en 2013 la tecnología inteligente apenas se había introducido en las tecnologías más básicas, y mucho menos en una operación de proceso tan compleja como una unidad de desalinización a bordo de un barco.
En 2021, lo que surgió de la investigación de la Armada se denomina MECO smartANALYTICS™ y está integrado en nuestras máquinas comerciales que prevalecen en toda la industria biofarmacéutica. La pandemia de COVID de 2020 arrojó una nueva luz sobre la importancia y la utilidad de la tecnología analítica. La capacidad de supervisar a distancia la maquinaria se emplea desde hace tiempo, al igual que la videoconferencia y una simple llamada telefónica. La ventaja de MECO smartANALYTICS™ es su capacidad para tener multitud de máquinas sobre el terreno, proporcionando un gran conjunto de datos, cada una con docenas de parámetros de proceso perfilándose frente a condiciones conocidas, reconociendo anomalías mínimas, tratando esas anomalías y alertando de problemas que de otro modo serían indetectables. El objetivo de la analítica es predecir el mantenimiento, maximizar la eficiencia operativa, mejorar la fiabilidad del sistema y minimizar el tiempo de inactividad. La monitorización remota por sí sola simplemente no es sostenible con respecto a los objetivos anteriores.
La experiencia COVID
MECO construyó la infraestructura necesaria para respaldar un programa de análisis comercial generalizado en 2016. Esto incluyó servidores seguros dedicados y la estandarización de la instrumentación de la maquinaria para proporcionar las entradas, salidas y comunicaciones necesarias. El software y la programación se desarrollaron de tal forma que están codificados dentro del sistema y pueden activarse si el cliente así lo decide. Algunas líneas de productos estándar, como los destiladores por compresión de vapor para la producción de agua para inyección y las máquinas de agua purificada MASTERpak™, tienen la tecnología y el hardware instalados.
Las restricciones y los protocolos de seguridad asociados a la pandemia mundial crearon cargas logísticas en el servicio físico rutinario. Las restricciones de viaje, las cuarentenas y otros problemas se tradujeron en retrasos y en la imposibilidad de estar físicamente presente cuando uno normalmente querría estarlo. Con la infraestructura ya instalada, es relativamente sencillo instalar el enlace de comunicación y activar los programas para que pueda utilizarse la tecnología smartANALYTICS™. La conversión se realiza en cuestión de días y los diagnósticos se ejecutan inmediatamente después. Esto ha resultado beneficioso desde varios puntos de vista.
En primer lugar, las visitas rutinarias que no se iban a realizar por motivos de seguridad se sustituyeron por la tranquilidad de saber que había un proceso analítico en marcha activado y una gran cantidad de recursos disponibles en el fabricante en caso necesario. Esas visitas rutinarias podían aplazarse con confianza.
En segundo lugar, la eliminación de la resolución de problemas in situ cuando surgen. Una agradable sorpresa es la intimidad que los fabricantes tenemos ahora con una instalación determinada. Nuestro conocimiento permanente de los parámetros del sistema suele traducirse en una resolución más rápida de los problemas. Las sorpresas y los servicios de emergencia se reducen en gran medida cuando se recurre a la analítica. Tenemos una visión más profunda de la maquinaria y una relación de colaboración con el personal del emplazamiento más estrecha que nunca.
Un elemento clave del éxito de un programa de análisis, más allá de la tecnología empleada, es la estandarización de los diseños de maquinaria y sistemas. Estas normas constituyen una base de conocimientos y datos a partir de la cual pueden establecerse perfiles significativos. Como tal, el fabricante tiene la ventaja de elaborar perfiles a partir de datos sustanciales, dada la mayor población de unidades sobre el terreno. Esto es algo que no es posible con diseños personalizados o perfiles analíticos de un único emplazamiento, como los que un cliente podría hacer por su cuenta.
Seguridad
Los problemas de seguridad representan el mayor obstáculo a la hora de implantar un programa de análisis. Es otro ámbito en el que el fabricante debe invertir mucho para garantizar la seguridad. Obviamente, el hardware físico y el enrutamiento de las comunicaciones deben realizarse de forma segura. La arquitectura debe configurarse de forma que el fabricante no tenga acceso a las redes SCADA, DCS, LAN o PLC de los clientes. Además, hay otras muchas consideraciones que deben tenerse en cuenta. ¿Qué datos se adquieren? ¿Son sensibles? ¿Están cifrados? ¿Hay dispositivos de almacenamiento extraíbles? ¿Existe una política de dispositivos móviles? ¿Qué tipo de acceso y seguridad tiene el personal in situ, en el fabricante o a través de terceros? ¿Existen políticas documentadas cuyo cumplimiento se audite periódicamente? Además de las comunicaciones físicas y la gestión de operaciones adecuadas, también son importantes las políticas de recursos humanos. ¿Están bien asignadas las funciones y responsabilidades en materia de seguridad? Deben existir acuerdos de confidencialidad y ética. Deben existir procesos establecidos para la incorporación, formación y cambio de estatus del personal en relación con la seguridad.
Informes
Los informes rutinarios y de intervención deben formar parte de cualquier paquete analítico. De este modo, tendrá la confianza de saber que todos los sistemas funcionan como deberían o si hay algún problema que requiera su atención. En nuestra opinión, el método de elaboración de informes descendente es el más eficaz. Aunque se analizan continuamente numerosos parámetros, se pueden resumir rápidamente y profundizar en ellos sólo si es necesario. La fiabilidad general del sistema, el consumo de energía y el mantenimiento pendiente son sólo algunos de ellos. Los procesos internos de información y comunicación de los fabricantes también deben ser eficaces. La necesidad de servicio debe ser proactiva, de modo que esté disponible cuando sea necesario. Los viejos tiempos en los que había que presentarse in situ para determinar cuál era el problema, pedir piezas, esperar a que llegaran y volver para solucionar el problema deberían desaparecer. Deben sustituirse por diagnósticos predictivos, contramedidas en tiempo real y una programación adecuada.
Resumen
Un verdadero programa de análisis no debe confundirse con lo que a menudo se denomina supervisión a distancia. Los productos bien desarrollados, combinados con los algoritmos adecuados, pueden sustituir a una supervisión reactiva menos eficaz. Deben establecerse procedimientos del sistema para la elaboración de informes, la seguridad y el mantenimiento proactivo. Todo el sector, incluidos los fabricantes de productos biológicos, los proveedores de sistemas y, en última instancia, los pacientes, sale ganando. Entre ellas se incluyen el ahorro de costes y tiempo, al tiempo que se garantiza la fiabilidad y se mejora la eficacia operativa. Las restricciones relacionadas con la pandemia mundial han aumentado el valor de la implantación de un programa de análisis. Los problemas de seguridad pueden abordarse específicamente con la infraestructura y las políticas adecuadas.