Otte år senere og erfaringerne med MECO smartANALYTICS™
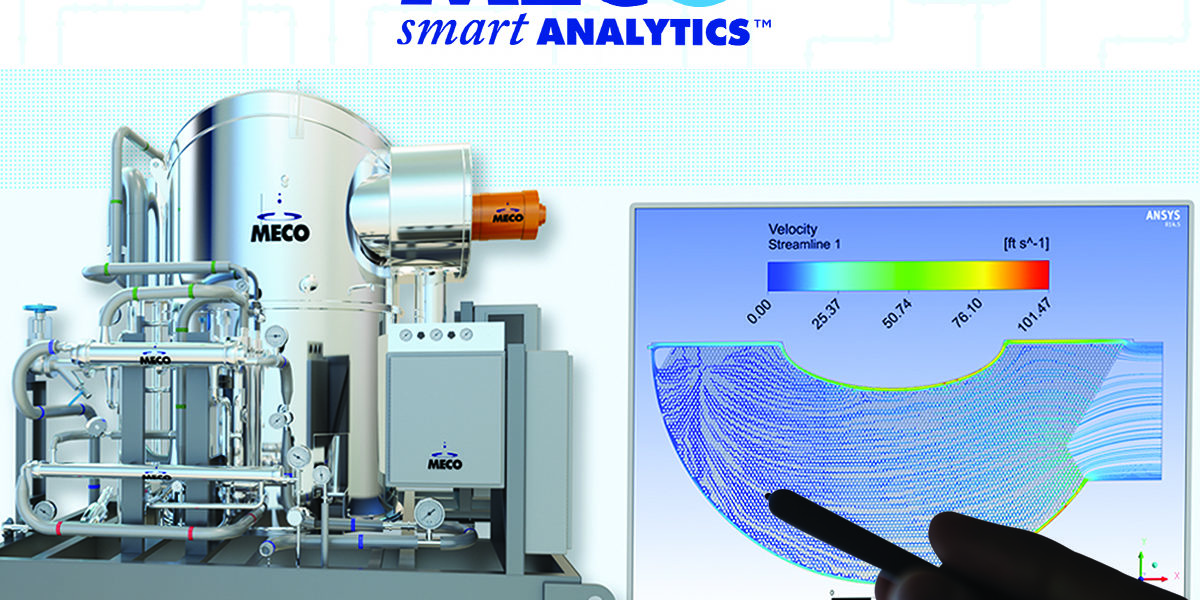
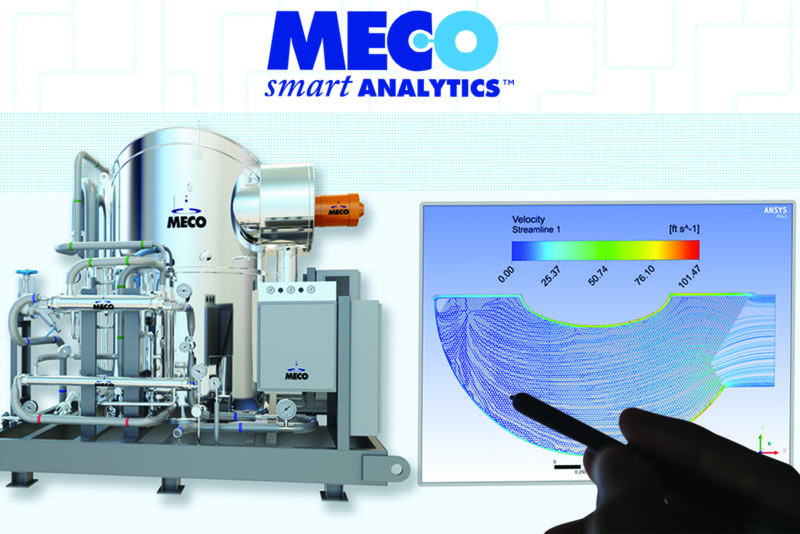
Skrevet af George Gsell, formand for MECO
I 2013 indgik den amerikanske flåde gennem Office of Naval Research og Naval Facilities Engineering Command en kontrakt med MECO om at designe og udvikle to modeller af avancerede afsaltningsenheder til skibe, som bl.a. skulle være helt autonome. Kompleksiteten og kravene til driften af afsaltningsanlæg til havvand betød, at maskinerne skulle kunne genkende interne procesparametre såvel som ydre miljøpåvirkninger og tilpasse sig skiftende forhold, så sømanden ikke behøvede at gribe ind i maskinen. Autonom kørsel er nu ved at blive en realitet, men i 2013 var smart teknologi knap nok blevet introduceret i de mest basale teknologier, og slet ikke i en så kompleks proces som en afsaltningsenhed om bord på et skib.
Spol hurtigt frem til 2021, og i dag kaldes det, der udsprang af flådens forskning, MEKA smartANALYTICS™ og er indlejret i vores kommercielle maskiner, der er udbredt i hele den biofarmaceutiske industri. COVID-pandemien i 2020 kastede et nyt lys over betydningen og nytten af analyseteknologi. Muligheden for at fjernovervåge maskiner har længe været anvendt, ligesom videokonferencer og et simpelt telefonopkald. Fordelen ved MECO smartANALYTICS™ er dens evne til at have en lang række maskiner i marken, der leverer et stort sæt data, hver med snesevis af procesparametre, der profilerer sig selv i forhold til kendte forhold, genkender små anomalier, håndterer disse anomalier og advarer om ellers uopdagelige problemer. Målet med analyse er at kunne forudsige vedligeholdelse, maksimere driftseffektiviteten, forbedre systemets pålidelighed og minimere nedetid. Fjernovervågning alene er simpelthen ikke bæredygtigt i forhold til de førnævnte mål.
COVID-oplevelsen
MECO opbyggede den nødvendige infrastruktur til at understøtte et udbredt kommercielt analyseprogram i 2016. Det omfattede dedikerede sikre servere og standardisering af instrumentering på maskiner til at levere de nødvendige indgange, udgange og kommunikation. Software og programmering blev udviklet, så det er kodet i systemet og kan aktiveres, hvis kunden vælger at gøre det. Visse standardproduktlinjer såsom dampkompressionsdestillatorer til produktion af vand til injektion og MASTERpak™Purified Water-maskiner har teknologien og hardwaren installeret.
Restriktionerne og sikkerhedsprotokollerne i forbindelse med den globale pandemi skabte logistiske byrder for rutinemæssig fysisk service. Rejserestriktioner, karantæner og andre problemer betød forsinkelser og manglende mulighed for at være fysisk til stede, når man normalt gerne ville være det. Når infrastrukturen allerede er på plads, er det en relativt enkel konvertering at installere kommunikationslinket og aktivere programmerne, så smartANALYTICS™-teknologienkan tages i brug. Konverteringen sker i løbet af få dage, og diagnosticeringen kører umiddelbart derefter. Det har vist sig at være en fordel fra flere synsvinkler.
For det første blev rutinebesøg, der ikke skulle finde sted af sikkerhedsmæssige årsager, erstattet med roen i sindet om, at der var en løbende analyseproces aktiveret og et væld af ressourcer til rådighed hos producenten, hvis det var nødvendigt. Disse rutinebesøg kunne udskydes med tillid.
For det andet var det slut med fejlfinding på stedet, når der opstår problemer. En behagelig overraskelse er den fortrolighed, vi som producenter nu har med et givet anlæg. Vores løbende viden om systemparametre betyder ofte, at problemerne løses hurtigere. Overraskelser og akut service er i høj grad reduceret, når analytics er involveret. Vi har en dybdegående indsigt i maskineriet og et bedre samarbejde med personalet på stedet end nogensinde før.
Et nøgleelement i et vellykket analyseprogram ud over den anvendte teknologi er standardisering af maskiner og systemdesign. Disse standarder danner en basislinje af viden og data, hvorfra meningsfuld profilering kan etableres. Som sådan har producenten fordelen af at profilere sig mod omfattende data i betragtning af den større population af enheder i marken. Det er noget, der ikke er muligt med specialdesign eller analytisk profilering af et enkelt anlæg, som en kunde kan gøre på egen hånd.
Sikkerhed
Sikkerhedsproblemer er den største forhindring for at implementere et analyseprogram. Det er endnu et område, hvor producenten er nødt til at investere meget for at sikre sikkerheden. Det er klart, at den fysiske hardware og kommunikationsrouting skal udføres på en sikker måde. Arkitekturen skal sættes op, så producenten ikke har adgang til kundernes SCADA-, DCS-, LAN- eller PLC-netværk. Derudover er der en lang række andre overvejelser, man bør gøre sig. Hvilke data indsamles, og er de følsomme? Er de krypterede? Er der flytbare lagringsenheder? Er der en politik for mobile enheder på plads? Hvilken personaleadgang og sikkerhed er der på stedet, hos producenten eller af tredjeparter? Er der dokumenterede politikker, som rutinemæssigt revideres for overholdelse? Ud over korrekt fysisk kommunikation og driftsstyring er politikker for menneskelige ressourcer også vigtige. Er roller og ansvar for sikkerhed fordelt korrekt? Aftaler om fortrolighed og etik bør være på plads. Der bør være etablerede processer for onboarding af personale, træning og ændring af status i forhold til sikkerhed.
Rapportering
Rutine- og interventionsrapportering bør være en del af enhver analysepakke. På den måde kan du være sikker på, at alle systemer fungerer, som de skal, eller om der er et problem, der kræver din opmærksomhed. Vi mener, at en top-down rapporteringsmetode er mest effektiv. Selvom mange parametre analyseres løbende, kan de hurtigt opsummeres og kun uddybes, hvis det er nødvendigt. Systemets overordnede pålidelighed, energiforbrug og ventende vedligeholdelse er blot nogle få. Producentens interne rapporterings- og kommunikationsprocesser bør også være effektive. Behovet for service bør være proaktivt, så de er tilgængelige, når der er behov for det. De gamle dage med at møde op på stedet for at finde ud af, hvad problemet er, bestille dele, vente på levering og vende tilbage for at løse et problem, bør elimineres. De bør erstattes af prædiktiv diagnostik, modforanstaltninger i realtid og korrekt planlægning.
Sammenfatning
Et ægte analyseprogram bør ikke forveksles med det, der ofte kaldes fjernovervågning. Veludviklede produkter kombineret med de rigtige algoritmer kan erstatte mindre effektiv reaktiv overvågning. Systemprocedurer for rapportering, sikkerhed og proaktiv vedligeholdelse bør være på plads. Der er fordele for hele branchen, herunder producenten af biologiske lægemidler, systemleverandøren og i sidste ende patienten. De omfatter besparelser i omkostninger og tid, samtidig med at pålideligheden sikres og driftseffektiviteten forbedres. Restriktionerne i forbindelse med den globale pandemi har øget værdien af implementeringen af et analyseprogram. Sikkerhedsproblemer kan håndteres specifikt med den rette infrastruktur og de rette politikker på plads.