Huit ans après, l'expérience de MECO smartANALYTICS™
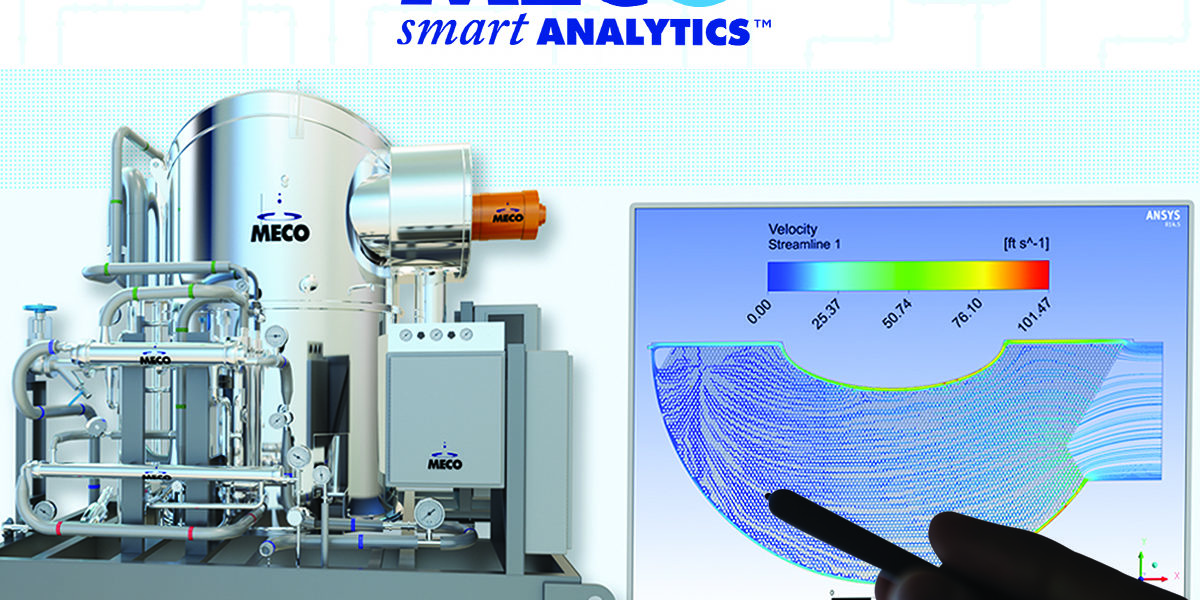
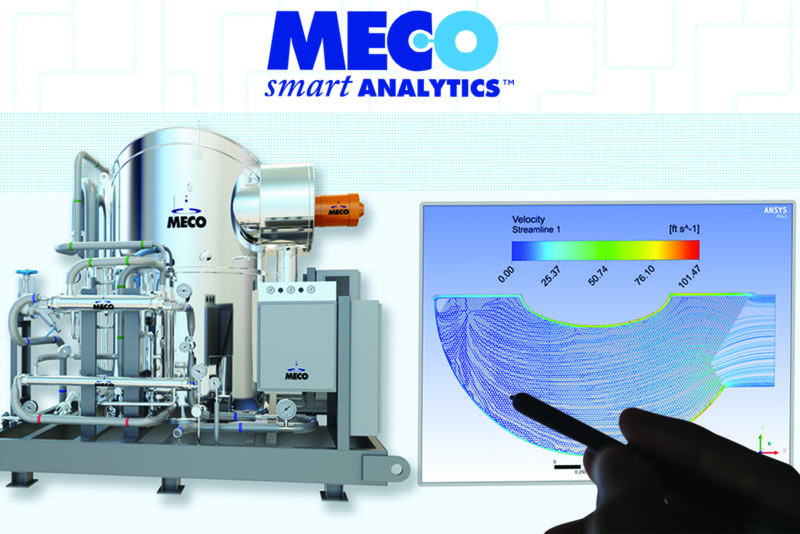
Rédigé par George Gsell, président du MECO
En 2013, la marine américaine, par l'intermédiaire de l'Office of Naval Research et du Naval Facilities Engineering Command, a demandé à MECO de concevoir et de développer deux modèles d'unités de dessalement avancées à bord des navires qui seraient, entre autres, complètement autonomes. En raison de la complexité et de la rigueur des opérations des unités de dessalement de l'eau de mer, les machines devaient reconnaître les paramètres internes du processus ainsi que les influences environnementales extérieures et s'adapter aux conditions changeantes de manière à ce que le marin n'ait aucune intervention à effectuer sur la machine. La conduite autonome devient aujourd'hui une réalité, mais en 2013, la technologie intelligente venait à peine d'être introduite dans les technologies les plus élémentaires, et encore moins dans un processus aussi complexe qu'une unité de dessalement à bord d'un navire.
Avance rapide jusqu'en 2021 et aujourd'hui, ce qui est né de la recherche de la Marine est appelé MECO smartANALYTICS™ et intégré dans nos machines commerciales répandues dans l'ensemble de l'industrie biopharmaceutique. La pandémie de COVID de 2020 a mis en lumière l'importance et l'utilité de la technologie analytique. La capacité de surveiller les machines à distance est utilisée depuis longtemps, tout comme la vidéoconférence et un simple appel téléphonique. L'avantage de MECO smartANALYTICS™ est sa capacité à disposer d'une multitude de machines sur le terrain, fournissant un grand ensemble de données, chacune avec des dizaines de paramètres de processus se profilant par rapport à des conditions connues, reconnaissant de minuscules anomalies, traitant ces anomalies et alertant sur des problèmes autrement indétectables. L'objectif de l'analyse est de prévoir la maintenance, de maximiser l'efficacité opérationnelle, d'améliorer la fiabilité du système et de minimiser les temps d'arrêt. La surveillance à distance seule n'est tout simplement pas viable en ce qui concerne les objectifs susmentionnés.
L'expérience COVID
MECO a mis en place l'infrastructure nécessaire pour soutenir un programme d'analyse commerciale à grande échelle en 2016. Cela comprenait des serveurs sécurisés dédiés et la normalisation de l'instrumentation sur les machines pour fournir les entrées, les sorties et la communication nécessaires. Le logiciel et la programmation ont été développés de manière à ce qu'ils soient codés dans le système et puissent être activés si le client le souhaite. Certaines lignes de produits standard, telles que les distillateurs à compression de vapeur pour la production d'eau pour injection et les machines MASTERpak™pour l'eau purifiée, sont équipées de la technologie et du matériel nécessaires.
Les restrictions et les protocoles de sécurité associés à la pandémie mondiale ont imposé des contraintes logistiques aux services physiques de routine. Les restrictions de voyage, les quarantaines et d'autres problèmes ont entraîné des retards et l'impossibilité d'être physiquement présent au moment où l'on voudrait normalement l'être. L'infrastructure étant déjà en place, il est relativement simple d'installer le lien de communication et d'activer les programmes de manière à ce que la technologie smartANALYTICS™puisse être engagée. La conversion s'effectue en quelques jours et les diagnostics sont exécutés immédiatement après. Cette solution s'est avérée bénéfique à plusieurs égards.
Tout d'abord, les visites de routine qui n'allaient pas avoir lieu pour des raisons de sécurité ont été remplacées par la tranquillité d'esprit de savoir qu'un processus d'analyse continu était activé et qu'une multitude de ressources étaient disponibles chez le fabricant en cas de besoin. Ces visites de routine ont pu être reportées en toute confiance.
Deuxièmement, l'élimination du dépannage sur place en cas de problème. Une surprise agréable est l'intimité que nous, fabricants, avons maintenant avec un site donné. Notre connaissance permanente des paramètres du système se traduit souvent par une résolution plus rapide des problèmes. Les surprises et les interventions d'urgence sont largement réduites lorsque l'on fait appel à l'analyse. Nous disposons d'une connaissance approfondie des machines et d'une relation de collaboration avec le personnel du site qui n'a jamais été aussi étroite.
Au-delà de la technologie employée, la normalisation de la conception des machines et des systèmes est un élément clé d'un programme d'analyse réussi. Ces normes constituent une base de connaissances et de données à partir de laquelle il est possible d'établir des profils significatifs. En tant que tel, le fabricant a l'avantage d'établir des profils à partir de données substantielles, étant donné le grand nombre d'unités sur le terrain. C'est quelque chose qui n'est pas possible avec des conceptions personnalisées uniques ou avec le profilage analytique d'un seul site tel qu'un client pourrait le faire lui-même.
Sécurité
Les problèmes de sécurité constituent le principal obstacle à la mise en œuvre d'un programme d'analyse. Il s'agit d'un autre domaine dans lequel le fabricant doit investir massivement pour garantir la sécurité. Il est évident que le matériel physique et le routage des communications doivent être sécurisés. L'architecture doit être configurée de manière à ce que le fabricant n'ait pas accès aux réseaux SCADA, DCS, LAN ou PLC des clients. En outre, il y a une foule d'autres considérations à prendre en compte. Quelles sont les données acquises et sont-elles sensibles ? Sont-elles cryptées ? Existe-t-il des dispositifs de stockage amovibles ? Existe-t-il une politique en matière d'appareils mobiles ? Quels sont l'accès et la sécurité du personnel sur place, chez le fabricant ou par des tiers ? Existe-t-il des politiques documentées dont la conformité fait l'objet d'audits réguliers ? Outre les communications physiques et la gestion des opérations, les politiques en matière de ressources humaines sont également importantes. Les rôles et les responsabilités en matière de sécurité sont-ils correctement répartis ? Des accords de non-divulgation et d'éthique doivent être mis en place. Des processus établis pour l'intégration du personnel, la formation et le changement de statut en matière de sécurité doivent être mis en place.
Rapports
Les rapports de routine et d'intervention devraient faire partie de tout progiciel d'analyse. De cette manière, vous aurez la certitude que tous les systèmes fonctionnent comme ils le devraient ou qu'il y a un problème qui requiert votre attention. Nous estimons qu'une méthode de reporting descendante est la plus efficace. Bien que de nombreux paramètres soient analysés en permanence, ils peuvent être résumés rapidement et approfondis uniquement si nécessaire. La fiabilité globale du système, la consommation d'énergie et la maintenance en cours n'en sont que quelques-uns. Les processus de communication et d'établissement de rapports internes des fabricants doivent également être efficaces. Le besoin de services doit être proactif, de sorte qu'ils soient disponibles en cas de besoin. Le temps où l'on se rendait sur place pour déterminer la nature du problème, où l'on commandait des pièces, où l'on attendait la livraison et où l'on revenait pour résoudre le problème doit être éliminé. Ils doivent être remplacés par des diagnostics prédictifs, des contre-mesures en temps réel et une programmation adéquate.
Résumé
Un véritable programme d'analyse ne doit pas être confondu avec ce que l'on appelle souvent la surveillance à distance. Des produits bien conçus, associés aux bons algorithmes, peuvent remplacer une surveillance réactive moins efficace. Des procédures de reporting, de sécurité et de maintenance proactive doivent être mises en place. L'industrie, y compris le fabricant de produits biologiques, le fournisseur de systèmes et, en fin de compte, le patient, en tirent des avantages. Il s'agit notamment d'économies de coûts et de temps, tout en garantissant la fiabilité et en améliorant l'efficacité opérationnelle. Les restrictions liées à la pandémie mondiale ont accru la valeur de la mise en œuvre d'un programme d'analyse. Les problèmes de sécurité peuvent être résolus de manière spécifique grâce à la mise en place d'une infrastructure et de politiques appropriées.