MEJORAR LA SOSTENIBILIDAD EN LA INDUSTRIA BIOFARMACÉUTICA
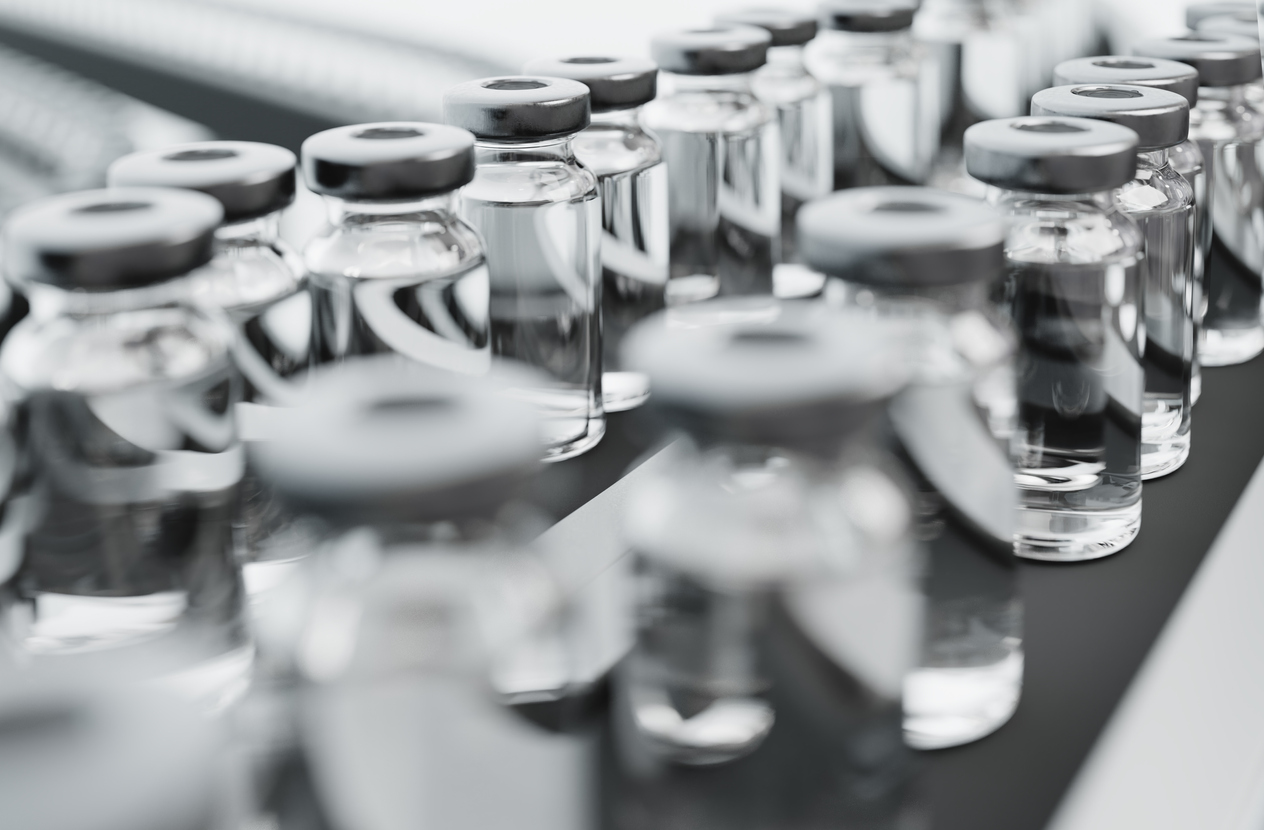
La producción eficiente de agua purificada y agua para inyección es clave para que la industria sea más sostenible
Aunque el objetivo principal de la industria biofarmacéutica es fabricar productos que mejoren la salud, el proceso de fabricación puede consumir mucha energía y generar emisiones y residuos perjudiciales para el medio ambiente y la salud humana. La industria también hace un uso intensivo del agua en una época de creciente escasez en la que cada gota cuenta. La industria biofarmacéutica es esencial para la medicina moderna. Es responsable de la investigación, el desarrollo y la fabricación de fármacos terapéuticos. Produce antibióticos y vacunas que salvan vidas y ha sido responsable del descubrimiento y desarrollo de productos y tecnologías sanitarios revolucionarios que incluyen el ADN recombinante y la terapia génica.
Impacto medioambiental de la fabricación biofarmacéutica
Aunque se acepta que los procesos de fabricación pueden tener un impacto directo en el medio ambiente y la salud del planeta, se han realizado muy pocos estudios sobre el impacto de la industria biofarmacéutica en particular. Pero sí se han realizado muchos estudios sobre la industria farmacéutica en general, que incluye los productos biofarmacéuticos. Según un estudio reciente, la industria farmacéutica produce muchas más emisiones de dióxido de carbono¹ que la industria automovilística. Otro estudio, que evaluaba el impacto medioambiental² del sistema sanitario de Estados Unidos y sus efectos sobre la salud pública, concluyó que la industria farmacéutica era responsable de una parte significativa de la contaminación atmosférica y sus impactos asociados, produciendo el 12% de la lluvia ácida, el 10% de las emisiones de gases de efecto invernadero, el 10% del smog, el 9% de los contaminantes atmosféricos, el 1-2% de las toxinas atmosféricas cancerígenas y no cancerígenas, y el 1% de la destrucción de ozono en la estratosfera. Aunque faltan estudios publicados, se han realizado esfuerzos para desarrollar formas de evaluar cuantitativamente el impacto medioambiental de los procesos de producción biofarmacéutica con métricas que incluyen la intensidad de la masa del proceso, la evaluación del ciclo de vida, la demanda acumulada de energía y el potencial de calentamiento global. La evaluación cuantitativa más simple, la intensidad de la masa del proceso (PMI), evalúa la eficiencia de un proceso de producción mediante la evaluación de la entrada de masa total, en kilogramos,
necesaria para producir 1 kilogramo de material de salida. Aunque la PMI no tiene en cuenta el consumo de energía ni otros factores medioambientales, resulta útil para comparar la eficiencia de dos procesos similares.
Una industria que consume mucha agua
Un informe reciente mostraba que el agua es el factor que más contribuye al impacto medioambiental del proceso de producción biofarmacéutica, con más del 90% del PMI.³ También se informó del impacto de la producción de Agua para Inyección (WFI), un ingrediente crítico en la fabricación de productos biofarmacéuticos. Utilizando la destilación convencional de efecto múltiple, se necesita un 70% más de recursos energéticos para producir WFI que con la destilación por compresión de vapor (VC).
El desarrollo de vacunas y medicamentos que salvan vidas requiere mucha agua.
Reducir el consumo y el despilfarro de agua
Es comprensible que la producción de WFI requiera mucha agua. El WFI debe superar rigurosos controles de calidad y el agua que no cumple los requisitos se desecha. Reducir el volumen de agua que se desperdicia puede reducir el consumo de agua y disminuir la huella hídrica de una empresa.
En los sistemas de ósmosis inversa (OI), el agua pasa a través de una membrana que retiene las moléculas más grandes que el tamaño de los poros de la membrana, junto con una parte del agua que no atraviesa la membrana. Esta agua, junto con los contaminantes presentes, se conoce como agua de rechazo. La destilación VC no sólo es eficiente desde el punto de vista energético, sino que también es el método más eficiente desde el punto de vista hídrico para producir WFI. Si consideramos un sistema de ósmosis inversa que normalmente tiene un caudal de alimentación de 37,5 litros por minuto, el caudal típico de agua de rechazo es de 12,1 litros por minuto. En comparación, un sistema de destilación de efecto múltiple (ME) tendría una tasa de alimentación de 35,6 litros por minuto y un caudal de agua de rechazo de 10,3 litros por minuto, mientras que un sistema VC de tamaño similar tendría una tasa de alimentación de 31,4 litros por minuto y un caudal de agua de rechazo de sólo 6,0 litros por minuto.
Además, en los sistemas de depuración basados en membranas, éstas deben limpiarse y desinfectarse periódicamente para evitar la acumulación de bacterias y biopelículas que pueden comprometer la calidad del agua. Los productos químicos utilizados para limpiar las membranas pueden causar daños medioambientales si se vierten con las aguas residuales sin un tratamiento adecuado.
Las membranas tienen una vida útil limitada y deben sustituirse periódicamente para garantizar su funcionamiento eficaz. Dado que las membranas desechadas acaban en los vertederos, los sistemas basados en membranas utilizan más consumibles y producen más residuos que los sistemas sin membranas.
Los sistemas de destilación VC están fabricados en acero inoxidable, que se considera un producto ecológico ya que puede reciclarse y reutilizarse una y otra vez. Los sistemas VC de MECO requieren un mantenimiento mínimo, eliminando la necesidad de consumibles a la vez que proporcionan una mayor fiabilidad y tiempos de funcionamiento más largos.
La solución basada en datos smartANALYTICS™ de MECO mantendrá el sistema funcionando con una eficiencia óptima maximizando la recuperación de agua pura y garantizando un uso óptimo del agua, la energía y los consumibles para reducir la huella hídrica de su empresa y mejorar su rendimiento medioambiental.
Reducir el consumo de energía
Actualmente, el WFI puede producirse utilizando cualquiera de los siguientes procesos: Destilación de Efecto Múltiple (ME), el más utilizado; Ósmosis Inversa (RO), electrodesionización y ultrafiltración; y destilación por Compresión de Vapor (VC). Los sistemas de ósmosis inversa basados en membranas ofrecen ventajas de coste inicial sobre la destilación ME. Son más eficientes energéticamente y tienen menores costes operativos. Pero los sistemas de destilación por compresión de vapor superan a ambos.
Compresión de vapor MECO con compresor GII Centurbo™.
Los destiladores VC pueden producir agua tanto a temperatura caliente (80°C) como a temperatura ambiente (~10-12°C por encima de la temperatura del agua de alimentación). El destilador puede ser conmutado entre el modo ambiente y la producción en caliente abriendo y cerrando la válvula alrededor del (de los) intercambiador(es) de calor del destilado. Un destilador a temperatura ambiente (frío) puede higienizar periódicamente el sistema de almacenamiento y distribución con el agua caliente del destilador, lo que representa una gran ventaja de este sistema. Los destiladores de CV ambiente también recuperan más calor y, por lo tanto, necesitan menos vapor de planta para funcionar que los que producen WFI caliente. A largo plazo, el VC es la opción más eficiente desde el punto de vista energético y económico para producir WFI. Los sistemas VC de MECO cuentan con evaporadores de gran superficie que consumen menos energía eléctrica. Y con el compresor GII Centurbo™ patentado por MECO, la destilación VC recupera y reutiliza el exceso de calor en las primeras etapas del proceso. El calor latente producido durante el proceso de evaporación se devuelve a un precalentador y a un demister para ayudar a alimentar estos procesos. La adición de intercambiadores de recuperación de calor a un destilador MECO VC mejora la economía a más del triple de la de los sistemas típicos de efecto múltiple o VC caliente.
o de efecto múltiple.
Como resultado, los sistemas VC consumen hasta un 70% menos de energía que los sistemas convencionales de destilación ME. Este ahorro de energía no sólo se traduce en un ahorro de costes, sino que también reduce significativamente las emisiones de dióxido de carbono asociadas a la producción de WFI, mejorando así el rendimiento medioambiental.
Reducir los costes a largo plazo
Aunque los costes iniciales asociados a la destilación VC pueden ser iguales o ligeramente superiores a los de los sistemas de ósmosis inversa basados en membranas, los costes de funcionamiento y mantenimiento a largo plazo son un 25% inferiores. También son más fiables, producen menos tiempos de inactividad y requieren menos mano de obra para su mantenimiento. A largo plazo, los sistemas basados en VC ofrecen la opción más eficiente desde el punto de vista energético, hídrico y económico para producir WFI.
El sistema MASTERfit de MECO utiliza un sistema simplificado de pretratamiento del descalcificador y del filtro de carbón de carbono simplificado y un CV MECO que utiliza un 20% menos de agua de alimentación y desecha un 65% menos de agua al desagüe.
Una asociación de confianza
Beneficios, Planeta, Personas. Al considerar estos tres pilares de la sostenibilidad, los sistemas de cadena de valor presentan ventajas definitivas. Generan mayores beneficios, envían menos residuos a los vertederos y tienen un menor impacto ambiental y en la salud que otros sistemas. La purificación del agua es esencial para la fabricación biofarmacéutica. En MECO, contamos con más de 90 años de experiencia en el suministro de soluciones de purificación de agua energéticamente eficientes que responden a prioridades medioambientales críticas. MECO sigue impulsando la innovación a través de la tecnología, el mejor servicio y productos de calidad. Asociarse con MECO puede apoyar los objetivos de sostenibilidad establecidos por las empresas biofarmacéuticas del sector. Póngase en contacto con nosotros hoy mismo para obtener más información sobre cómo podemos ayudar a sus instalaciones a alcanzar sus objetivos de sostenibilidad.
Referencias
1. Belkhir, Lotfi, et al. "Carbon Footprint of the Global Pharmaceutical Industry and Relative Impact of Its
Principales actores". Journal of Cleaner Production, 14 dic. 2018, www.sciencedirect.com/science/article/abs/
pii/S0959652618336084.
2. Eckelman, Matthew J., y Jodi Sherman. "Environmental Impacts of the U.S. Health Care System
y efectos en la salud pública". PLOS ONE, journals.plos.org/plosone/article?id=10.1371%2Fjournal.
pone.0157014. Consultado el 14 de julio de 2023.
3. Kokai-Kun, John. "¿Cuál es el impacto medioambiental de la fabricación continua biofarmacéutica?
Part I". What's The Environmental Impact Of Biopharma Continuous Manufacturing Part I, www.
bioprocessonline.com/doc/what-s-the-environmental-impact-of-biopharma-continuous-manufacturingpart-
i-0001. Consultado el 14 de julio de 2023.