IMPROVING SUSTAINABILITY IN THE BIOPHARMACEUTICAL INDUSTRY
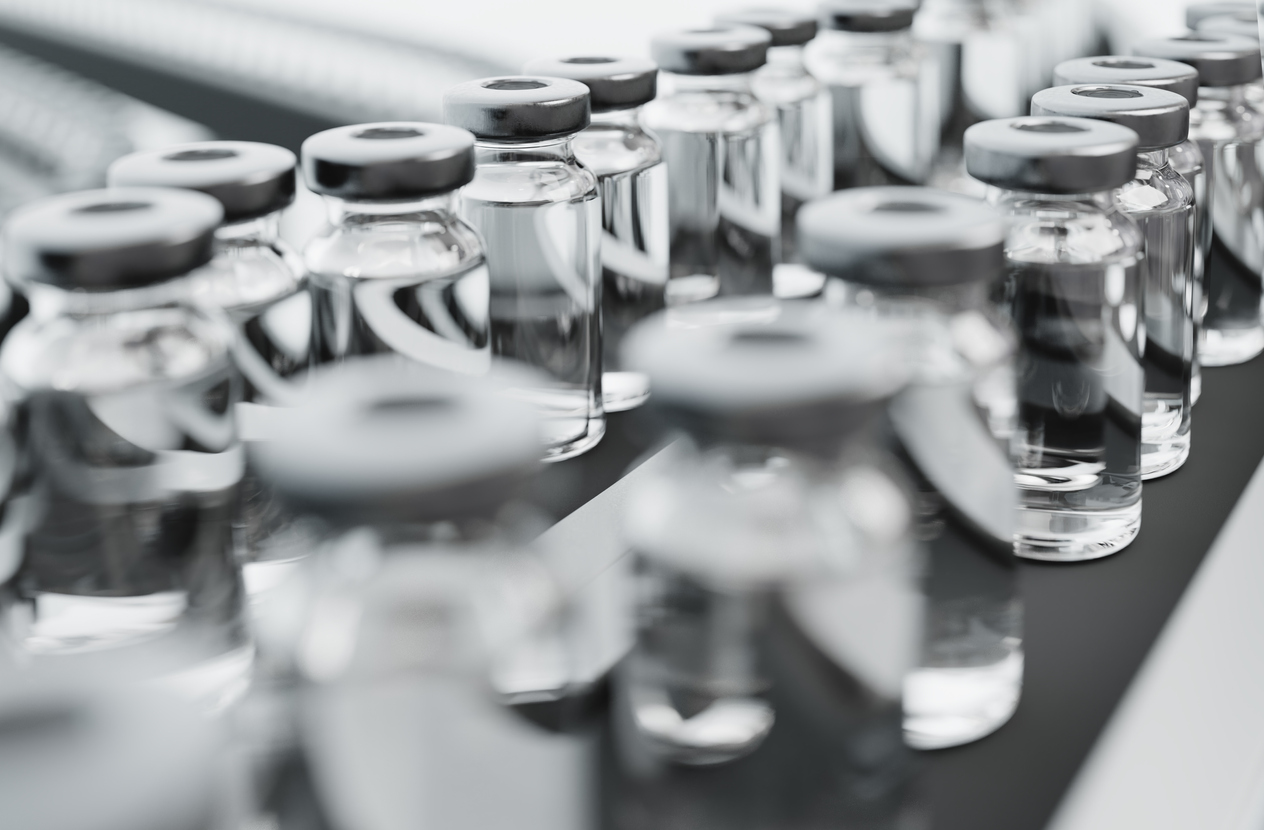
Efficiently producing Purified Water and Water for Injection is key to making the industry more sustainable
While the biopharmaceutical industry’s primary focus is on producing products that improve health, the manufacturing process can be energy-intensive and can produce emissions and waste products that are detrimental to both environmental and human health. The industry is also water-intensive in a time of increasing water scarcity when every drop counts. The biopharmaceutical industry is essential to modern medicine. It’s responsible for researching, developing, and manufacturing therapeutic drugs. It produces life-saving antibiotics and vaccines and has been responsible for the discovery and development of revolutionary health products and technologies that include recombinant DNA and gene therapy.
Environmental Impact of Biopharmaceutical Manufacturing
While it’s accepted that manufacturing processes can have a direct impact on the environment and the health of the planet, there have been very few studies on the biopharmaceutical industry’s impact in particular. But there have been many studies on the wider pharmaceutical industry, which includes biopharmaceuticals. One recent study found the pharmaceutical industry produces significantly more carbon dioxide emissions¹ than the automotive industry. Another study, which assessed the environmental impacts² of the United States’ health care system and its effects on public health, found that the pharmaceutical industry accounted for a significant portion of atmospheric pollution and its associated impacts, producing 12% of acid rain, 10% of greenhouse gas emissions, 10% of smog, 9% of air pollutants, 1-2% of carcinogenic and noncarcinogenic air toxins, and 1% of ozone depletion in the stratosphere. While published studies may be lacking, there have been efforts to develop ways to quantitatively assess the environmental impact of biopharmaceutical production processes with metrics including process mass intensity, life cycle assessment, cumulative energy demand, and global warming potential. The simplest quantitative assessment, process mass intensity (PMI), evaluates the efficiency of a production process by assessing the total mass input, in kilograms,
required for it to produce 1 kilogram of output material. While PMI does not consider energy consumption and other environmental factors, it is useful for comparing the efficiency of two similar processes.
A Water-Intensive Industry
A recent report showed that water is the single biggest contributing factor to the environmental impact of the biopharmaceutical production process, accounting for more than 90% of the PMI.³ Also reported was the impact of producing Water for Injection (WFI), a critical ingredient in the manufacture of biopharmaceuticals. Using conventional multiple effect distillation, it takes 70% more energy resources to produce WFI than Vapor Compression (VC) distillation.
Developing vaccines and life-savings medicines is water intensive.
Reducing Water Use and Waste
Producing WFI is understandably very water-intensive. WFI needs to pass rigorous quality control standards and any water that doesn’t meet the grade is discarded. Reducing the volume of water that is wasted can reduce water usage and lower a company’s water footprint.
In Reverse Osmosis (RO) systems, water passes through a membrane that retains molecules larger than the pore size of the membrane, along with a portion of the water that does not pass through the membrane. This water, together with the contaminants present, is known as reject water. VC distillation is not only energy-efficient, it is also the most water-efficient method of producing WFI. If you consider an RO system that typically has a feed rate of 37.5 liters per minute then the typical reject water flow rate is 12.1 liters per minute. By comparison, a Multiple Effect (ME) distillation system would have a feed rate of 35.6 liters per minute and a reject water flow rate of 10.3 liters per minute, while a similarly sized VC system would have a feed rate of 31.4 liters per minute and a reject water flow rate of just 6.0 liters per minute.
Furthermore, in membrane-based purification systems, the membranes must be cleaned and sanitized regularly to prevent the buildup of bacteria and biofilms that can compromise water quality. The chemicals used to clean membranes can cause environmental harm if they are discharged with wastewater without appropriate treatment.
Membranes have a limited lifespan and must be replaced periodically to ensure they efficiently function. Because discarded membranes ultimately end up in landfills, membrane-based systems use more consumables and produce more waste than membrane-free systems.
VC distillation systems are manufactured from stainless steel, which is considered a green product since it can be recycled and reused over and over. MECO’s VC systems require minimal maintenance, eliminating the need for consumables while providing improved reliability and longer runtimes.
MECO’s smartANALYTICS™ data-driven solution will keep the system operating at optimal efficiency by maximizing pure water recovery and ensuring optimal use of water, energy, and consumables to reduce your company’s water footprint and improve your environmental performance.
Reducing Energy Consumption
Currently, WFI can be produced using any of the following processes: Multiple Effect (ME) distillation, the most commonly used; Reverse Osmosis (RO), electrodeionization, and ultrafiltration; and Vapor Compression (VC) distillation. Membrane-based RO systems offer initial cost advantages over ME distillation. They are more energy efficient and have lower operational costs. But VC distillation systems outperform them both.
MECO vapor compression with GII Centurbo™ compressor.
VC stills can produce water at both hot (80°C) and ambient temperatures (~10-12°C above feed water temperature). The distiller can be switched between ambient mode and hot production by opening and closing the valve around the distillate heat exchanger(s). An ambient (cold) VC still can periodically sanitize the storage and distribution system with hot water from the distiller, a major advantage of this system. Ambient VC stills also recover more heat and therefore require less plant steam to operate than those that produce WFI hot. Over the long term, VC is the most energy-efficient and cost-efficient option for producing WFI. MECO’s VC systems feature large surface area evaporators that use less electrical power. And with MECO’s patented GII Centurbo™ Compressor, VC distillation recovers and reuses excess heat in the early stages of the process. Latent heat produced during the evaporation process is returned to a preheater and demister to help power these processes. Adding heat recovery exchangers to a MECO VC distiller improves the economy to more than 3x that of typical multiple effect
or hot VC systems.
As a result, VC systems use as much as 70% less energy than conventional ME distillation systems. These energy savings not only translate into cost savings but also significantly reduce carbon dioxide emissions associated with the production of WFI, thereby improving environmental performance.
Reducing Long-Term Costs
While upfront costs associated with VC distillation may be the same or slightly higher than those of membrane-based RO systems, long-term operating and maintenance costs are 25% lower. They are also more reliable, produce less downtime, and require less manpower to maintain. Over the long term, VC-based systems offer the most energy-efficient, water-efficient, and cost-efficient option for producing WFI.
MECO’s MASTERfit system utilizes a simplifed water softener and carbon filter pretreatment system coupled with a MECO VC using 20% less feedwater and rejecting 65% less water to drain.
A Trusted Partnership
Profits, Planet, People. When considering these three pillars of sustainability, VC systems hold definitive advantages. They generate higher profits, send less waste to landfills, and have lower environmental impacts and associated health impacts than other systems. Water purification is essential for biopharmaceutical manufacturing. At MECO, we have more than 90 years of experience in providing energy-efficient water purification solutions that are responsive to critical environmental priorities. MECO continues to push innovation forward through technology, best-in-class service, and quality products. Partnering with MECO can support sustainability goals set by biopharmaceutical companies in the industry. Get in touch with us today to learn more about how we can help your facility meet your sustainability goals.
References
1. Belkhir, Lotfi, et al. “Carbon Footprint of the Global Pharmaceutical Industry and Relative Impact of Its
Major Players.” Journal of Cleaner Production, 14 Dec. 2018, www.sciencedirect.com/science/article/abs/
pii/S0959652618336084.
2. Eckelman, Matthew J., and Jodi Sherman. “Environmental Impacts of the U.S. Health Care System
and Effects on Public Health.” PLOS ONE, journals.plos.org/plosone/article?id=10.1371%2Fjournal.
pone.0157014. Accessed 14 July 2023.
3. Kokai-Kun, John. “What’s the Environmental Impact of Biopharma Continuous Manufacturing?
Part I.” What’s The Environmental Impact Of Biopharma Continuous Manufacturing Part I, www.
bioprocessonline.com/doc/what-s-the-environmental-impact-of-biopharma-continuous-manufacturingpart-
i-0001. Accessed 14 July 2023.