MELHORAR A SUSTENTABILIDADE NA INDÚSTRIA BIOFARMACÊUTICA
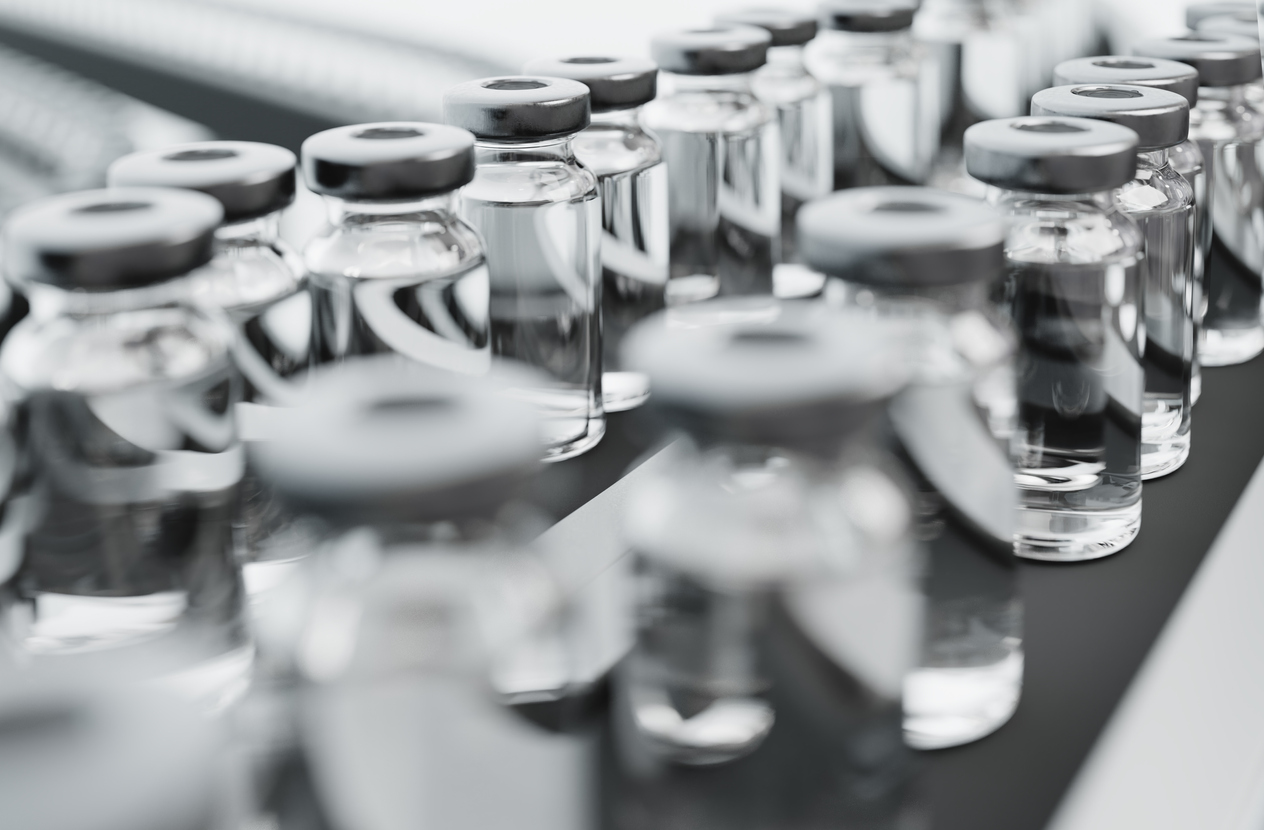
Produzir água purificada e água para injeção de forma eficiente é fundamental para tornar a indústria mais sustentável
Embora o principal objetivo da indústria biofarmacêutica seja a produção de produtos que melhorem a saúde, o processo de fabrico pode ser intensivo em termos energéticos e pode produzir emissões e resíduos que são prejudiciais tanto para o ambiente como para a saúde humana. A indústria também consome muita água numa época de crescente escassez de água, em que cada gota conta. A indústria biofarmacêutica é essencial para a medicina moderna. É responsável pela investigação, desenvolvimento e fabrico de medicamentos terapêuticos. Produz antibióticos e vacinas que salvam vidas e tem sido responsável pela descoberta e desenvolvimento de produtos e tecnologias de saúde revolucionários que incluem o ADN recombinante e a terapia genética.
Impacto ambiental do fabrico de produtos biofarmacêuticos
Embora se reconheça que os processos de fabrico podem ter um impacto direto no ambiente e na saúde do planeta, foram realizados muito poucos estudos sobre o impacto da indústria biofarmacêutica em particular. Mas há muitos estudos sobre a indústria farmacêutica em geral, que inclui os produtos biofarmacêuticos. Um estudo recente concluiu que a indústria farmacêutica produz significativamente mais emissões de dióxido de carbono¹ do que a indústria automóvel. Outro estudo, que avaliou os impactos ambientais² do sistema de cuidados de saúde dos Estados Unidos e os seus efeitos na saúde pública, concluiu que a indústria farmacêutica era responsável por uma parte significativa da poluição atmosférica e dos seus impactos associados, produzindo 12% das chuvas ácidas, 10% das emissões de gases com efeito de estufa, 10% do smog, 9% dos poluentes atmosféricos, 1-2% das toxinas atmosféricas cancerígenas e não cancerígenas e 1% da destruição do ozono na estratosfera. Embora possam faltar estudos publicados, tem havido esforços para desenvolver formas de avaliar quantitativamente o impacte ambiental dos processos de produção biofarmacêutica com métricas que incluem a intensidade da massa do processo, a avaliação do ciclo de vida, a procura cumulativa de energia e o potencial de aquecimento global. A avaliação quantitativa mais simples, a intensidade da massa do processo (PMI), avalia a eficiência de um processo de produção através da avaliação da massa total de entrada, em quilogramas,
necessária para produzir 1 quilograma de material de saída. Embora a PMI não considere o consumo de energia e outros factores ambientais, é útil para comparar a eficiência de dois processos semelhantes.
Uma indústria com utilização intensiva de água
Um relatório recente mostrou que a água é o fator que mais contribui para o impacto ambiental do processo de produção biofarmacêutica, representando mais de 90% do PMI.³ Foi também relatado o impacto da produção de água para injeção (WFI), um ingrediente crítico no fabrico de produtos biofarmacêuticos. Utilizando a destilação convencional de múltiplos efeitos, são necessários mais 70% de recursos energéticos para produzir WFI do que a destilação por compressão de vapor (VC).
O desenvolvimento de vacinas e de medicamentos que salvam vidas é intensivo em água.
Reduzir a utilização e o desperdício de água
A produção de WFI é, compreensivelmente, muito intensiva em termos de água. A WFI tem de passar por rigorosos padrões de controlo de qualidade e qualquer água que não atinja o grau é descartada. Reduzir o volume de água desperdiçada pode reduzir o consumo de água e diminuir a pegada hídrica de uma empresa.
Nos sistemas de Osmose Inversa (OR), a água passa através de uma membrana que retém moléculas maiores do que o tamanho dos poros da membrana, juntamente com uma parte da água que não passa através da membrana. Esta água, juntamente com os contaminantes presentes, é conhecida como água rejeitada. A destilação VC não é apenas eficiente em termos energéticos, é também o método mais eficiente em termos de água para produzir WFI. Se considerarmos um sistema RO que normalmente tem um caudal de alimentação de 37,5 litros por minuto, o caudal típico da água de rejeição é de 12,1 litros por minuto. Em comparação, um sistema de destilação de efeito múltiplo (ME) teria uma taxa de alimentação de 35,6 litros por minuto e uma taxa de fluxo de água rejeitada de 10,3 litros por minuto, enquanto um sistema VC de tamanho semelhante teria uma taxa de alimentação de 31,4 litros por minuto e uma taxa de fluxo de água rejeitada de apenas 6,0 litros por minuto.
Além disso, nos sistemas de purificação baseados em membranas, as membranas devem ser limpas e higienizadas regularmente para evitar a acumulação de bactérias e biofilmes que podem comprometer a qualidade da água. Os produtos químicos utilizados para limpar as membranas podem causar danos ambientais se forem descarregados com as águas residuais sem tratamento adequado.
As membranas têm um tempo de vida limitado e devem ser substituídas periodicamente para garantir o seu funcionamento eficiente. Uma vez que as membranas descartadas acabam por ir parar a aterros, os sistemas baseados em membranas utilizam mais consumíveis e produzem mais resíduos do que os sistemas sem membranas.
Os sistemas de destilação VC são fabricados em aço inoxidável, que é considerado um produto ecológico, uma vez que pode ser reciclado e reutilizado vezes sem conta. Os sistemas VC da MECO requerem uma manutenção mínima, eliminando a necessidade de consumíveis e proporcionando uma maior fiabilidade e tempos de funcionamento mais longos.
A solução orientada por dados smartANALYTICS™ da MECO manterá o sistema a funcionar com a eficiência ideal, maximizando a recuperação de água pura e garantindo a utilização ideal de água, energia e consumíveis para reduzir a pegada hídrica da sua empresa e melhorar o seu desempenho ambiental.
Reduzir o consumo de energia
Atualmente, a WFI pode ser produzida utilizando qualquer um dos seguintes processos: Destilação de efeito múltiplo (ME), o mais utilizado; Osmose inversa (RO), electrodeionização e ultrafiltração; e destilação por compressão de vapor (VC). Os sistemas de RO baseados em membranas oferecem vantagens de custo inicial em relação à destilação ME. São mais eficientes em termos energéticos e têm custos operacionais mais baixos. Mas os sistemas de destilação VC superam ambos.
Compressão de vapor MECO com compressor GII Centurbo™.
Os alambiques VC podem produzir água tanto a quente (80°C) como à temperatura ambiente (~10-12°C acima da temperatura da água de alimentação). O destilador pode ser comutado entre o modo ambiente e a produção a quente, abrindo e fechando a válvula à volta do(s) permutador(es) de calor do destilado. Um alambique de circuito fechado ambiente (frio) pode higienizar periodicamente o sistema de armazenamento e distribuição com água quente proveniente do destilador, o que constitui uma grande vantagem deste sistema. Os alambiques de VC ambiente também recuperam mais calor e, por isso, necessitam de menos vapor para funcionar do que os que produzem WFI quente. A longo prazo, o VC é a opção mais eficiente em termos de energia e de custos para a produção de WFI. Os sistemas de VC da MECO apresentam evaporadores de grande área de superfície que usam menos energia elétrica. E com o Compressor GII Centurbo™ patenteado pela MECO, a destilação VC recupera e reutiliza o excesso de calor nas fases iniciais do processo. O calor latente produzido durante o processo de evaporação é devolvido a um pré-aquecedor e desembaçador para ajudar a alimentar esses processos. A adição de trocadores de recuperação de calor a um destilador MECO VC melhora a economia para mais de 3x a de sistemas típicos de efeito múltiplo
ou sistemas VC quentes.
Como resultado, os sistemas VC utilizam até 70% menos energia do que os sistemas convencionais de destilação ME. Estas poupanças de energia não só se traduzem em poupanças de custos, como também reduzem significativamente as emissões de dióxido de carbono associadas à produção de WFI, melhorando assim o desempenho ambiental.
Reduzir os custos a longo prazo
Embora os custos iniciais associados à destilação VC possam ser os mesmos ou ligeiramente superiores aos dos sistemas RO baseados em membranas, os custos de funcionamento e manutenção a longo prazo são 25% inferiores. São também mais fiáveis, produzem menos tempo de inatividade e requerem menos mão de obra para a sua manutenção. A longo prazo, os sistemas baseados em VC oferecem a opção mais eficiente em termos energéticos, de água e de custos para a produção de WFI.
O sistema MASTERfit da MECO utiliza um sistema simplificado de pré-tratamento do amaciador de água e do filtro de carbono e filtro de carbono simplificados, juntamente com um MECO VC que utiliza menos 20% de água de alimentação e rejeita menos 65% de água para drenagem.
Uma parceria de confiança
Lucros, Planeta, Pessoas. Ao considerar estes três pilares da sustentabilidade, os sistemas de CV têm vantagens definitivas. Geram lucros mais elevados, enviam menos resíduos para aterros e têm menos impactos ambientais e impactos na saúde associados do que outros sistemas. A purificação da água é essencial para o fabrico biofarmacêutico. Na MECO, temos mais de 90 anos de experiência no fornecimento de soluções de purificação de água com eficiência energética que respondem a prioridades ambientais críticas. A MECO continua a impulsionar a inovação através da tecnologia, do melhor serviço e de produtos de qualidade. A parceria com a MECO pode apoiar os objectivos de sustentabilidade definidos pelas empresas biofarmacêuticas do sector. Entre em contacto connosco hoje para saber mais sobre como podemos ajudar as suas instalações a atingir os seus objectivos de sustentabilidade.
Referências
1. Belkhir, Lotfi, et al. "Carbon Footprint of the Global Pharmaceutical Industry and Relative Impact of Its Major Players.
Major Players." Journal of Cleaner Production, 14 de dezembro de 2018, www.sciencedirect.com/science/article/abs/
pii/S0959652618336084.
2. Eckelman, Matthew J., e Jodi Sherman. "Environmental Impacts of the U.S. Health Care System
e efeitos sobre a saúde pública". PLOS ONE, journals.plos.org/plosone/article?id=10.1371%2Fjournal.
pone.0157014. Acedido em 14 de julho de 2023.
3. Kokai-Kun, John. "Qual é o impacto ambiental do fabrico contínuo de produtos biofarmacêuticos?
Parte I". What's The Environmental Impact Of Biopharma Continuous Manufacturing Part I (Qual é o impacto ambiental da produção contínua biofarmacêutica? Parte I), www.
bioprocessonline.com/doc/what-s-the-environmental-impact-of-biopharma-continuous-manufacturingpart-
i-0001. Acedido em 14 de julho de 2023.