VERBESSERUNG DER NACHHALTIGKEIT IN DER BIOPHARMAZEUTISCHEN INDUSTRIE
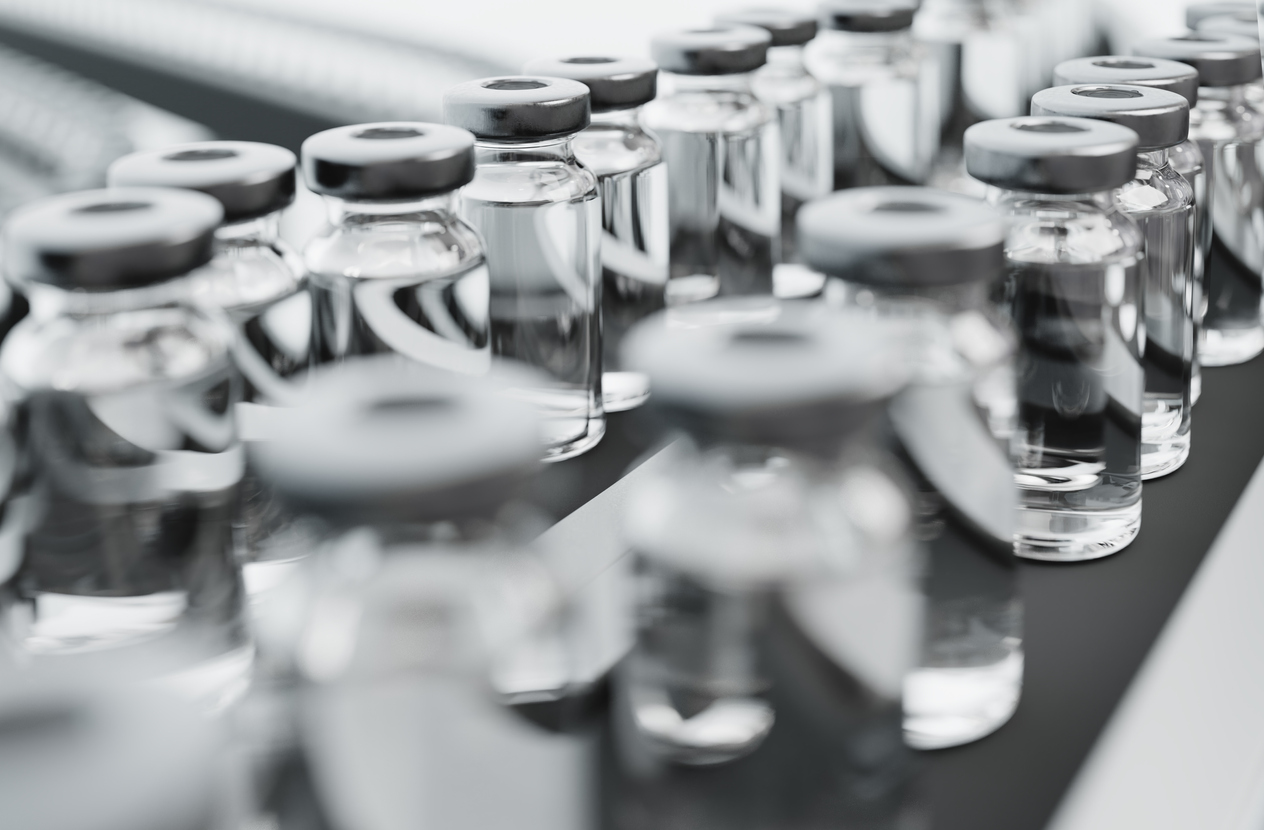
Effiziente Produktion von gereinigtem Wasser und Wasser für Injektionszwecke ist der Schlüssel zu einer nachhaltigeren Industrie
Die biopharmazeutische Industrie konzentriert sich zwar in erster Linie auf die Herstellung von Produkten, die die Gesundheit verbessern, doch der Herstellungsprozess kann energieintensiv sein und Emissionen und Abfallprodukte erzeugen, die sowohl für die Umwelt als auch für die menschliche Gesundheit schädlich sind. In einer Zeit zunehmender Wasserknappheit, in der jeder Tropfen zählt, ist die Branche auch sehr wasserintensiv. Die biopharmazeutische Industrie ist für die moderne Medizin unverzichtbar. Sie ist für die Erforschung, Entwicklung und Herstellung von therapeutischen Medikamenten verantwortlich. Sie stellt lebensrettende Antibiotika und Impfstoffe her und war für die Entdeckung und Entwicklung revolutionärer Gesundheitsprodukte und -technologien wie rekombinanter DNA und Gentherapie verantwortlich.
Umweltauswirkungen der biopharmazeutischen Herstellung
Es ist zwar bekannt, dass Herstellungsprozesse direkte Auswirkungen auf die Umwelt und die Gesundheit des Planeten haben können, aber es gibt nur sehr wenige Studien über die Auswirkungen der biopharmazeutischen Industrie im Besonderen. Es gibt jedoch viele Studien über die pharmazeutische Industrie im Allgemeinen, zu der auch Biopharmazeutika gehören. Eine kürzlich durchgeführte Studie ergab, dass die pharmazeutische Industrie deutlich mehr Kohlendioxidemissionen¹ verursacht als die Autoindustrie. Eine andere Studie, die die Umweltauswirkungen² des Gesundheitssystems der Vereinigten Staaten und seine Auswirkungen auf die öffentliche Gesundheit untersuchte, kam zu dem Ergebnis, dass die pharmazeutische Industrie einen erheblichen Anteil an der Luftverschmutzung und den damit verbundenen Auswirkungen hat: 12 % des sauren Regens, 10 % der Treibhausgasemissionen, 10 % des Smogs, 9 % der Luftschadstoffe, 1-2 % der krebserregenden und nicht krebserregenden Luftgifte und 1 % des Ozonabbaus in der Stratosphäre. Auch wenn es an veröffentlichten Studien mangelt, gibt es Bemühungen, die Umweltauswirkungen biopharmazeutischer Produktionsprozesse quantitativ zu bewerten, u. a. anhand der Prozessmassenintensität, der Lebenszyklusanalyse, des kumulativen Energiebedarfs und des globalen Erwärmungspotenzials. Die einfachste quantitative Bewertung, die Prozessmassenintensität (PMI), bewertet die Effizienz eines Produktionsprozesses, indem sie den gesamten Masseninput in Kilogramm bewertet,
der erforderlich ist, um 1 Kilogramm Ausgangsmaterial zu produzieren. Obwohl die PMI den Energieverbrauch und andere Umweltfaktoren nicht berücksichtigt, ist sie nützlich, um die Effizienz zweier ähnlicher Prozesse zu vergleichen.
Eine wasserintensive Industrie
Ein kürzlich veröffentlichter Bericht hat gezeigt, dass Wasser der größte Einzelfaktor für die Umweltauswirkungen des biopharmazeutischen Produktionsprozesses ist und mehr als 90 % des PMI ausmacht.³ Berichtet wurde auch über die Auswirkungen der Herstellung von Wasser für Injektionszwecke (Water for Injection, WFI), einem wichtigen Bestandteil bei der Herstellung von Biopharmazeutika. Bei der herkömmlichen Mehrstufen-Destillation werden 70 % mehr Energieressourcen für die Herstellung von WFI benötigt als bei der Vapor Compression (VC)-Destillation.
Die Entwicklung von Impfstoffen und lebensrettenden Medikamenten ist wasserintensiv.
Reduzierung von Wasserverbrauch und -verschwendung
Die Herstellung von WFI ist verständlicherweise sehr wasserintensiv. WFI muss strenge Qualitätskontrollstandards erfüllen, und Wasser, das nicht den Anforderungen entspricht, wird weggeworfen. Die Verringerung der Wassermenge, die verschwendet wird, kann den Wasserverbrauch reduzieren und den Wasserfußabdruck eines Unternehmens verringern.
Bei der Umkehrosmose (RO) wird das Wasser durch eine Membran geleitet, die Moleküle zurückhält, die größer als die Porengröße der Membran sind, zusammen mit einem Teil des Wassers, der nicht durch die Membran gelangt. Dieses Wasser wird zusammen mit den vorhandenen Verunreinigungen als Ausschusswasser bezeichnet. Die VC-Destillation ist nicht nur energieeffizient, sondern auch die wassersparendste Methode zur Herstellung von WFI. Bei einem Umkehrosmose-System, das in der Regel eine Zufuhrrate von 37,5 Litern pro Minute hat, beträgt die typische Durchflussrate des Rejektwassers 12,1 Liter pro Minute. Im Vergleich dazu hat ein ME-Destillationssystem (Multiple Effect) eine Zuführungsrate von 35,6 Litern pro Minute und eine Ausschusswasserdurchflussrate von 10,3 Litern pro Minute, während ein VC-System ähnlicher Größe eine Zuführungsrate von 31,4 Litern pro Minute und eine Ausschusswasserdurchflussrate von nur 6,0 Litern pro Minute hat.
Außerdem müssen die Membranen in membranbasierten Klärsystemen regelmäßig gereinigt und desinfiziert werden, um die Ansammlung von Bakterien und Biofilmen zu verhindern, die die Wasserqualität beeinträchtigen können. Die zur Reinigung der Membranen verwendeten Chemikalien können die Umwelt schädigen, wenn sie ohne entsprechende Behandlung mit dem Abwasser abgeleitet werden.
Membranen haben eine begrenzte Lebensdauer und müssen regelmäßig ausgetauscht werden, damit sie effizient funktionieren. Da weggeworfene Membranen letztlich auf Mülldeponien landen, verbrauchen membranbasierte Systeme mehr Verbrauchsmaterialien und produzieren mehr Abfall als membranfreie Systeme.
VC-Destillationssysteme werden aus rostfreiem Stahl hergestellt, der als umweltfreundliches Produkt gilt, da er recycelt und immer wieder verwendet werden kann. Die VC-Systeme von MECO erfordern nur einen minimalen Wartungsaufwand, wodurch der Bedarf an Verbrauchsmaterialien entfällt, während sie gleichzeitig eine höhere Zuverlässigkeit und längere Laufzeiten bieten.
Die datengesteuerte Lösung smartANALYTICS™ von MECO sorgt dafür, dass das System mit optimaler Effizienz arbeitet, indem es die Rückgewinnung von reinem Wasser maximiert und die optimale Nutzung von Wasser, Energie und Verbrauchsmaterialien sicherstellt, um den Wasserverbrauch Ihres Unternehmens zu reduzieren und Ihre Umweltbilanz zu verbessern.
Senkung des Energieverbrauchs
Derzeit kann WFI mit einem der folgenden Verfahren hergestellt werden: Mehrfacheffektdestillation (ME), das am häufigsten verwendete Verfahren; Umkehrosmose (RO), Elektrodeionisation und Ultrafiltration; und Dampfkompressionsdestillation (VC). Auf Membranen basierende RO-Systeme bieten anfängliche Kostenvorteile gegenüber der ME-Destillation. Sie sind energieeffizienter und haben niedrigere Betriebskosten. VC-Destillationssysteme übertreffen jedoch beide.
MECO-Dampfverdichtung mit GII Centurbo™-Kompressor.
VC-Destillierapparate können sowohl heißes Wasser (80°C) als auch Wasser bei Umgebungstemperatur (~10-12°C über der Speisewassertemperatur) produzieren. Der Destillator kann durch Öffnen und Schließen des Ventils um den/die Destillatwärmetauscher herum zwischen Umgebungsbetrieb und Heißproduktion umgeschaltet werden. Eine kalte VC-Brennerei kann das Lager- und Verteilungssystem regelmäßig mit heißem Wasser aus der Brennerei reinigen, was ein großer Vorteil dieses Systems ist. Ambient VC-Brennereien gewinnen auch mehr Wärme zurück und benötigen daher weniger Anlagendampf für den Betrieb als solche, die WFI heiß produzieren. Langfristig gesehen ist VC die energie- und kosteneffizienteste Option zur Herstellung von WFI. Die VC-Systeme von MECO verfügen über Verdampfer mit großer Oberfläche, die weniger Strom verbrauchen. Und mit dem patentierten GII Centurbo™-Kompressor von MECO wird bei der VC-Destillation überschüssige Wärme in den frühen Phasen des Prozesses zurückgewonnen und wiederverwendet. Latente Wärme, die während des Verdampfungsprozesses entsteht, wird in einen Vorwärmer und einen Demister zurückgeführt, um diese Prozesse zu unterstützen. Durch den Einbau von Wärmerückgewinnungswärmetauschern in eine MECO-VC-Destillationsanlage wird die Wirtschaftlichkeit um mehr als das Dreifache im Vergleich zu typischen Mehrfacheffekt
oder heißen VC-Systemen.
Infolgedessen verbrauchen VC-Systeme bis zu 70 % weniger Energie als herkömmliche ME-Destillationssysteme. Diese Energieeinsparungen führen nicht nur zu Kosteneinsparungen, sondern verringern auch die mit der Herstellung von WFI verbundenen Kohlendioxidemissionen erheblich und verbessern so die Umweltbilanz.
Langfristige Kosten senken
Während die Anfangskosten der VC-Destillation gleich oder etwas höher sind als die von membranbasierten Umkehrosmoseanlagen, sind die langfristigen Betriebs- und Wartungskosten um 25 % niedriger. Sie sind außerdem zuverlässiger, verursachen weniger Ausfallzeiten und erfordern weniger Personal für die Wartung. Langfristig gesehen bieten VC-basierte Systeme die energie-, wasser- und kosteneffizienteste Option zur Herstellung von WFI.
Das MASTERfit-System von MECO besteht aus einem vereinfachten Wasserenthärter und Kohlefilter Vorbehandlungssystem in Verbindung mit einem MECO VC, das 20 % weniger Speisewasser verbraucht und 65 % weniger Wasser in den Abfluss ableitet.
Eine vertrauensvolle Partnerschaft
Profite, Planet, Menschen. Wenn man diese drei Säulen der Nachhaltigkeit betrachtet, haben VC-Systeme eindeutige Vorteile. Sie erwirtschaften höhere Gewinne, verursachen weniger Abfall auf Deponien und haben geringere Umwelt- und Gesundheitsauswirkungen als andere Systeme. Die Wasseraufbereitung ist für die biopharmazeutische Produktion unerlässlich. MECO verfügt über mehr als 90 Jahre Erfahrung in der Bereitstellung energieeffizienter Wasseraufbereitungslösungen, die den kritischen Umweltprioritäten Rechnung tragen. MECO treibt die Innovation durch Technologie, erstklassigen Service und Qualitätsprodukte weiter voran. Eine Partnerschaft mit MECO kann die Nachhaltigkeitsziele von biopharmazeutischen Unternehmen in der Branche unterstützen. Setzen Sie sich noch heute mit uns in Verbindung, um mehr darüber zu erfahren, wie wir Ihrem Unternehmen helfen können, seine Nachhaltigkeitsziele zu erreichen.
Referenzen
1. Belkhir, Lotfi, et al. "Carbon Footprint of the Global Pharmaceutical Industry and Relative Impact of Its
Major Players." Journal of Cleaner Production, 14. Dez. 2018, www.sciencedirect.com/science/article/abs/.
pii/S0959652618336084.
2. Eckelman, Matthew J., und Jodi Sherman. "Umweltauswirkungen des US-Gesundheitswesens
and Effects on Public Health". PLOS ONE, journals.plos.org/plosone/article?id=10.1371%2Fjournal.
pone.0157014. Abgerufen am 14. Juli 2023.
3. Kokai-Kun, John. "Welche Auswirkungen hat die kontinuierliche Herstellung von Biopharmazeutika auf die Umwelt?
Part I." What's The Environmental Impact Of Biopharma Continuous Manufacturing Part I, www.
bioprocessonline.com/doc/what-s-the-environmental-impact-of-biopharma-continuous-manufacturingpart-
i-0001. Abgerufen am 14. Juli 2023.