AMÉLIORER LA DURABILITÉ DANS L'INDUSTRIE BIOPHARMACEUTIQUE
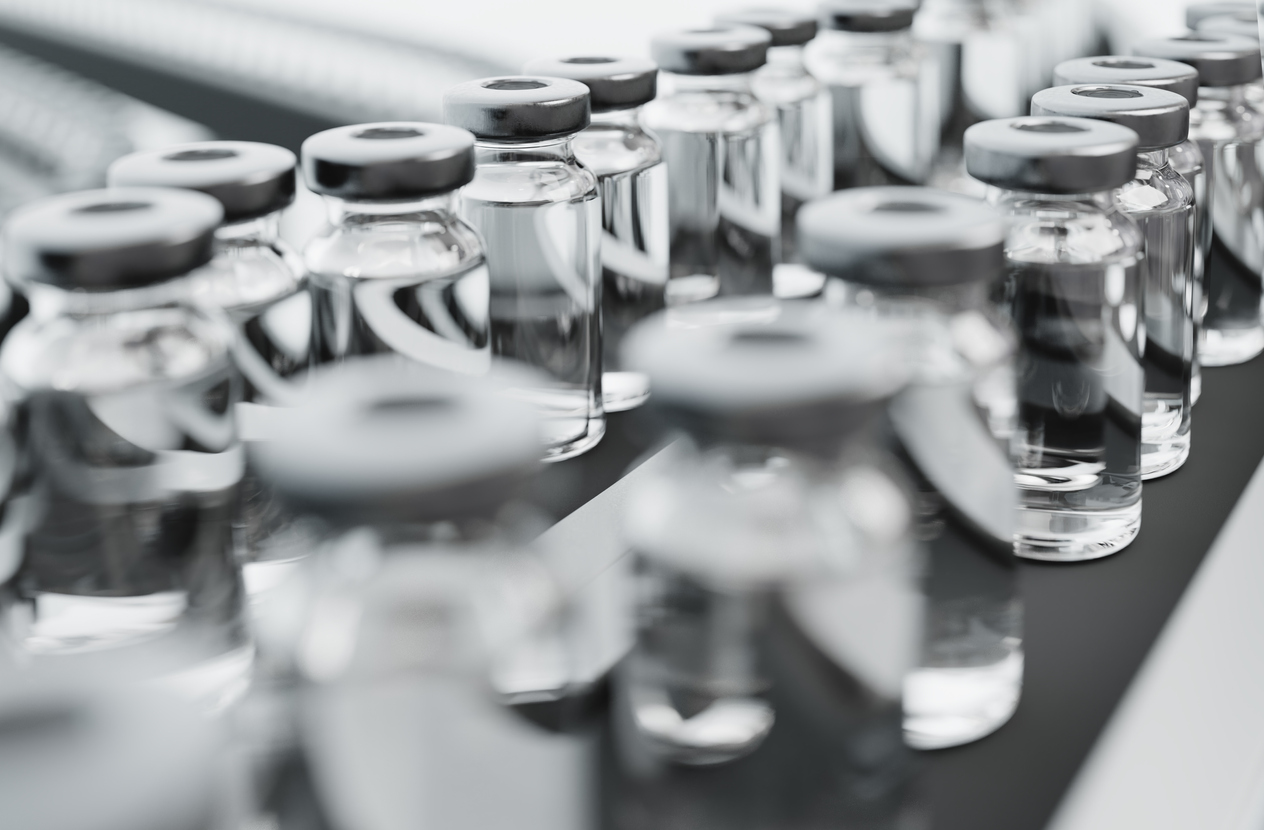
La production efficace d'eau purifiée et d'eau pour préparations injectables est essentielle pour rendre l'industrie plus durable.
Bien que l'industrie biopharmaceutique se concentre principalement sur la fabrication de produits qui améliorent la santé, le processus de fabrication peut être énergivore et produire des émissions et des déchets qui nuisent à la fois à l'environnement et à la santé humaine. L'industrie est également gourmande en eau, à une époque où celle-ci se fait de plus en plus rare et où chaque goutte compte. L'industrie biopharmaceutique est essentielle à la médecine moderne. Elle est responsable de la recherche, du développement et de la fabrication de médicaments thérapeutiques. Elle produit des antibiotiques et des vaccins qui sauvent des vies et est à l'origine de la découverte et du développement de produits et de technologies de santé révolutionnaires, dont l'ADN recombinant et la thérapie génique.
Impact environnemental de la fabrication de produits biopharmaceutiques
S'il est admis que les processus de fabrication peuvent avoir un impact direct sur l'environnement et la santé de la planète, très peu d'études ont été menées sur l'impact de l'industrie biopharmaceutique en particulier. En revanche, de nombreuses études ont été menées sur l'industrie pharmaceutique au sens large, qui comprend les produits biopharmaceutiques. Une étude récente a montré que l'industrie pharmaceutique produit beaucoup plus d'émissions de dioxyde de carbone¹ que l'industrie automobile. Une autre étude, qui a évalué les impacts environnementaux² du système de soins de santé des États-Unis et ses effets sur la santé publique, a révélé que l'industrie pharmaceutique était responsable d'une part importante de la pollution atmosphérique et de ses impacts associés, produisant 12 % des pluies acides, 10 % des émissions de gaz à effet de serre, 10 % du smog, 9 % des polluants atmosphériques, 1 à 2 % des toxines atmosphériques cancérigènes et non cancérigènes, et 1 % de l'appauvrissement de la couche d'ozone dans la stratosphère. Malgré l'absence d'études publiées, des efforts ont été déployés pour mettre au point des méthodes d'évaluation quantitative de l'impact environnemental des processus de production biopharmaceutique à l'aide de paramètres tels que l'intensité massique du processus, l'évaluation du cycle de vie, la demande énergétique cumulée et le potentiel de réchauffement planétaire. L'évaluation quantitative la plus simple, l'intensité massique du processus (PMI), évalue l'efficacité d'un processus de production en déterminant la masse totale, en kilogrammes, nécessaire pour produire 1 kilogramme,
nécessaire pour produire 1 kilogramme de matière en sortie. Bien que l'IMP ne prenne pas en compte la consommation d'énergie et d'autres facteurs environnementaux, elle est utile pour comparer l'efficacité de deux processus similaires.
Une industrie gourmande en eau
Un rapport récent a montré que l'eau est le principal facteur contribuant à l'impact environnemental du processus de production biopharmaceutique, puisqu'elle représente plus de 90 % de l'indice de performance (PMI). En utilisant la distillation conventionnelle à effets multiples, il faut 70 % de ressources énergétiques en plus pour produire de l'eau pour injection que la distillation par compression de vapeur (VC).
La mise au point de vaccins et de médicaments vitaux nécessite beaucoup d'eau.
Réduire la consommation d'eau et les déchets
La production de WFI est naturellement très gourmande en eau. La WFI doit satisfaire à des normes rigoureuses de contrôle de la qualité et toute eau qui ne répond pas à ces normes est rejetée. La réduction du volume d'eau gaspillée permet de réduire la consommation d'eau et de diminuer l'empreinte hydrique d'une entreprise.
Dans les systèmes d'osmose inverse (OI), l'eau passe à travers une membrane qui retient les molécules plus grandes que la taille des pores de la membrane, ainsi qu'une partie de l'eau qui ne passe pas à travers la membrane. Cette eau, ainsi que les contaminants présents, est connue sous le nom d'eau rejetée. La distillation VC n'est pas seulement économe en énergie, c'est aussi la méthode de production de WFI la plus économe en eau. Si l'on considère un système d'OI dont le débit d'alimentation est généralement de 37,5 litres par minute, le débit de l'eau rejetée est généralement de 12,1 litres par minute. En comparaison, un système de distillation à effets multiples (ME) a un débit d'alimentation de 35,6 litres par minute et un débit d'eau rejetée de 10,3 litres par minute, tandis qu'un système VC de taille similaire a un débit d'alimentation de 31,4 litres par minute et un débit d'eau rejetée de seulement 6,0 litres par minute.
En outre, dans les systèmes d'épuration par membrane, les membranes doivent être nettoyées et désinfectées régulièrement pour éviter l'accumulation de bactéries et de biofilms susceptibles de compromettre la qualité de l'eau. Les produits chimiques utilisés pour nettoyer les membranes peuvent nuire à l'environnement s'ils sont rejetés avec les eaux usées sans traitement approprié.
Les membranes ont une durée de vie limitée et doivent être remplacées périodiquement pour assurer leur bon fonctionnement. Étant donné que les membranes mises au rebut finissent dans les décharges, les systèmes à membrane utilisent plus de consommables et produisent plus de déchets que les systèmes sans membrane.
Les systèmes de distillation VC sont fabriqués en acier inoxydable, considéré comme un produit écologique puisqu'il peut être recyclé et réutilisé à l'infini. Les systèmes VC de MECO nécessitent un entretien minimal, éliminant le besoin de consommables tout en offrant une fiabilité accrue et des durées de fonctionnement plus longues.
La solution smartANALYTICS™ de MECO, pilotée par les données, maintiendra le système en fonctionnement à une efficacité optimale en maximisant la récupération de l'eau pure et en assurant une utilisation optimale de l'eau, de l'énergie et des consommables afin de réduire l'empreinte hydrique de votre entreprise et d'améliorer votre performance environnementale.
Réduire la consommation d'énergie
Actuellement, le WFI peut être produit à l'aide de l'un des procédés suivants : La distillation à effets multiples (ME), la plus couramment utilisée ; l'osmose inverse (RO), l'électrodéionisation et l'ultrafiltration ; et la distillation par compression de vapeur (VC). Les systèmes d'OI à base de membranes offrent des avantages en termes de coûts initiaux par rapport à la distillation ME. Ils sont plus efficaces sur le plan énergétique et leurs coûts d'exploitation sont moins élevés. Mais les systèmes de distillation par compression de vapeur sont plus performants que ces deux types de systèmes.
Compression de vapeur MECO avec compresseur GII Centurbo™.
Les distillateurs VC peuvent produire de l'eau à la fois à chaud (80°C) et à température ambiante (~10-12°C au-dessus de la température de l'eau d'alimentation). Le distillateur peut être commuté entre le mode ambiant et la production d'eau chaude en ouvrant et en fermant la vanne autour de l'échangeur de chaleur du distillat. Un alambic VC ambiant (froid) peut périodiquement assainir le système de stockage et de distribution avec de l'eau chaude provenant du distillateur, ce qui constitue un avantage majeur de ce système. Les alambics VC ambiants récupèrent également plus de chaleur et nécessitent donc moins de vapeur d'eau pour fonctionner que ceux qui produisent de l'eau chaude WFI. À long terme, le VC est l'option la plus efficace sur le plan énergétique et la plus rentable pour la production de WFI. Les systèmes VC de MECO sont dotés d'évaporateurs à grande surface qui consomment moins d'énergie électrique. Et grâce au compresseur GII Centurbo™ breveté de MECO, la distillation VC récupère et réutilise l'excès de chaleur dès les premières étapes du processus. La chaleur latente produite pendant le processus d'évaporation est renvoyée vers un préchauffeur et un désembueur pour aider à alimenter ces processus. L'ajout d'échangeurs de récupération de chaleur à un distillateur MECO VC permet de tripler l'économie par rapport aux systèmes typiques à effet multiple ou à effet chaud.
ou des systèmes VC chauds.
Par conséquent, les systèmes VC consomment jusqu'à 70 % d'énergie en moins que les systèmes de distillation ME conventionnels. Ces économies d'énergie se traduisent non seulement par des économies de coûts, mais aussi par une réduction significative des émissions de dioxyde de carbone associées à la production de WFI, améliorant ainsi les performances environnementales.
Réduire les coûts à long terme
Si les coûts initiaux associés à la distillation VC peuvent être identiques ou légèrement supérieurs à ceux des systèmes d'OI à membrane, les coûts d'exploitation et de maintenance à long terme sont inférieurs de 25 %. Ils sont également plus fiables, entraînent moins de temps d'arrêt et nécessitent moins de main-d'œuvre pour leur entretien. À long terme, les systèmes à base de VC constituent l'option la plus efficace en termes d'énergie, d'eau et de coûts pour la production de WFI.
Le système MASTERfit de MECO utilise un système simplifié de prétraitement de l'adoucisseur d'eau et du filtre à charbon, couplé à un VC MECO. de prétraitement simplifié couplé à un VC MECO utilisant 20 % d'eau d'alimentation en moins et rejetant 65 % d'eau en moins à l'égout.
Un partenariat de confiance
Profits, Planète, Personnes. Si l'on considère ces trois piliers de la durabilité, les systèmes de CV présentent des avantages indéniables. Ils génèrent des profits plus élevés, envoient moins de déchets dans les décharges et ont moins d'impacts environnementaux et d'effets sur la santé que les autres systèmes. La purification de l'eau est essentielle pour la fabrication de produits biopharmaceutiques. Chez MECO, nous avons plus de 90 ans d'expérience dans la fourniture de solutions de purification de l'eau efficaces sur le plan énergétique et répondant aux priorités environnementales essentielles. MECO continue de faire progresser l'innovation grâce à la technologie, à un service de premier ordre et à des produits de qualité. En s'associant à MECO, les entreprises biopharmaceutiques de l'industrie peuvent atteindre leurs objectifs de développement durable. Contactez-nous dès aujourd'hui pour en savoir plus sur la manière dont nous pouvons aider votre établissement à atteindre ses objectifs de développement durable.
Références
1. Belkhir, Lotfi, et al. "Carbon Footprint of the Global Pharmaceutical Industry and Relative Impact of Its
Major Players". Journal of Cleaner Production, 14 déc. 2018, www.sciencedirect.com/science/article/abs/
pii/S0959652618336084.
2. Eckelman, Matthew J., et Jodi Sherman. Impacts environnementaux du système de santé américain et effets sur la santé publique".
et effets sur la santé publique". PLOS ONE, journals.plos.org/plosone/article?id=10.1371%2Fjournal.
pone.0157014. Consulté le 14 juillet 2023.
3. Kokai-Kun, John. "Quel est l'impact environnemental de la fabrication continue dans le secteur biopharmaceutique ?
Part I." What's The Environmental Impact Of Biopharma Continuous Manufacturing Part I, www.
bioprocessonline.com/doc/what-s-the-environmental-impact-of-biopharma-continuous-manufacturingpart-
i-0001. Consulté le 14 juillet 2023.