Data Analytics for Water Industry
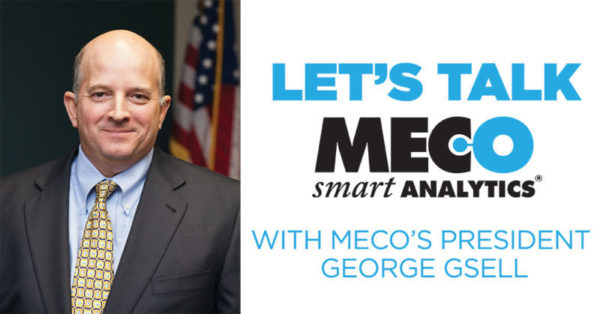
MECO smartANALYTICS™ is a data profiling and analytics tool that connects and analyzes data from water purification plants to improve operational efficiency and reliability. The data collected is profiled against design standards and other plants in the field. MECO smartANALYTICS™ enables MECO’s engineers to recommend operational best practices to ensure that each plant is operating in the most efficient and cost-advantageous manner.
George V. Gsell is the President of Mechanical Equipment Company (MECO), a leading manufacturer of engineered equipment for water purification. The company has a 90-year history and a broad base of products for desalination and water purification. Mr. Gsell shares his thoughts on MECO smartANALYTICS™, Big Data and Water.
Big data and IoT are being applied on pumps, water meters and other industrial components. MECO has been investing in analytics for water systems. Why? What impact can the application of big data have on water purification?
Among other things, big data has the ability to ensure the reliability and quality of a water supply. I suspect most people think about their municipal supply of tap water when there is a reference to water purification. Certainly municipal supplies of tap water are an important resource, but throughout industry, the purification of water from non-traditional sources and for other uses is exceptionally important. In some cases, tap water is unavailable or the quality is not sufficient. For example, if you were on a Navy ship or an offshore oil platform, surrounded by the ocean, you would know that the desalination plants below deck are critical not only to the crew’s potable water supply but also to the vessels operating systems, which require a very high level of purity. The logistics of basic services become much more difficult, and a supply of freshwater is not taken for granted. Another example is the manufacture of life saving drugs in the biopharmaceutical industry where ultra-pure water is the primary ingredient. In these applications and industries, such as power generation, food and beverage and others, water is considered a critical component. Its quality and reliable supply are vitally important. Water is purified by machinery or systems, and there is no readily available alternative. A failure in the supply or quality of the water can have significant consequences.
What factors influence a system’s reliability that might lead to issues of availability or quality?
The machinery and systems used to produce water can be complex, and many operate under harsh conditions. Regardless of the process employed, water purification systems for various industries require the use of expensive materials, such as specialized membranes, high grade stainless steels, titanium and other alloys. While operating, the machinery is subjected to fouling from colloidal matter and organics in raw water supplies as well as scaling from minerals. The raw water is normally concentrated and sometimes evaporated at elevated temperatures. Cleanings are often necessary and may use acids, caustics, detergents or oxidants, all of which are detrimental to the equipment over time and may have an environmental impact. Corrosion, maintenance and downtime are issues to be dealt with. Routine maintenance is required and big data will ideally help us foresee and address our customer’s needs instead of reacting to a phone call or email.
There are various techniques used to manufacture pure water. Membranes under high pressure are sometimes used, and in other applications, evaporators, ion exchange units or particulate filters are the major components. Each process will also use a host of critical ancillary items, such as high pressure pumps, energy recovery devices, compressors, chemical injection systems, transfer pumps, valves, programmable logic controllers (PLCs) and other components. A problem with any of the ancillary items often results in a system wide problem, which can be a precursor to a more serious issue related to water quality or system reliability. Data acquisition is sometimes used for routine monitoring and trend analysis. In these cases, the operator oversight and intervention is generally quite high. Excursions from normal operating conditions generate alarms sometimes resulting in a shutdown. Data analytics provide a more proactive means of operating a water system in the best manner possible. We are looking through significant amounts of data for small changes that are indicative of a future issue.
MECO’s terminology for the application of big data is smartANALYTICS™. Is there any significance to that or is it similar to other component applications we just mentioned?
Our application of is not one of a component but of a system comprised of many components. Insights and understanding, not only to the components operation, but to the interaction of those components and the system as a whole is key to smartANALYTICS™. We have standard system designs, so being able to map and mirror a system’s actual performance to its design criteria and our experience with other similar systems helps inform us and the client.
Aside from reliability and quality, what “other things” that you referenced can big data and MECO smartANALYTICS™ impact?
Operational efficiency is an area we are focused on, because the operating costs of purifying water are larger than the initial cost of the plant. Sustainability is another area where we expect to have an impact. The client interaction is important as well. Through analytics, reporting and dialog we have a stronger bond and a sharing of knowledge with our customers based upon data and experiences.
Can you give us an example of how smartANALYTICS™ is used on MECO water plants?
Today, our detailed design parameters are well documented. Profiling operating data against this design information can give early insights into problems before they arise. For example, a smart system knows the power consumption of a motor as well as its speed, voltage, amperage, temperature and vibration level. More importantly, a smart system knows what these parameters should be under various conditions. They can be profiled relative to the design and other similar systems in the field such that abnormalities can be identified and diagnosed. Early detection can avoid more costly, unplanned interruptions later and extend the operational life until maintenance can be scheduled.
We also know the expected differential pressure and regeneration frequency of a particular filter element based upon certain raw water conditions and our design parameters. A variation from an expected performance could be from a change in the raw water supply, or it may indicate a problem with the quality or quantity of a chemical being injected upstream. Typically, there are multiple unit operations within a water purification system, and it is up to the operator to see that these are all functioning properly for the system to operate effectively. We are solely focused on water purification. It is all we do. This means we can provide expertise and services for our clients in an efficient manner.
What impact does smartANALYTICS™ have on manpower requirements and do you see it replacing the need for operators?
The U.S. Navy, through the Office of Naval Research, has funded programs for the development of Advanced Shipboard Desalination Systems that will ideally use data analytics to support autonomous operation of shipboard desalination systems. The goal is to substantially reduce the sailor’s involvement in the operation of the desalination unit and to eliminate the maintenance associated with the equipment during deployment. While seemingly a reasonable objective, it is a tall order considering the operating parameters and constraints on-board a Navy ship and the rigors of seawater desalination. We have not been successful in reducing normal operator intervention, but certainly one day we would expect to have an impact. The current expectations for industrial applications, from MECO’s perspective, are that we can be predictive such that we can plan the workload and be more responsive to needs as opposed to being reactive.
How does MECO’s involvement aid in the operation of the plants?
As the manufacturer of the system we have the knowledge and expertise in-house for routine operations, including a working knowledge of water chemistry and specific unit functions. Even if we did not actually manufacture the system, we are able to supplement internal teams who are perhaps stretched thin or suffering from turnover. Operator training is one way we have transferred knowledge to aid the users of their systems. Our in-house expertise is derived from a wide base of systems installed, and we can utilize that base of data and experience to better serve clients on the operation of individual plants. Small variations in data might be below an alarm limit and go unnoticed by an operator, but the deviation may be consistent with a variable known to the manufacturer, who has access to a larger population of plants.
MECO has promoted its smartANALYTICS™ program as a source of improvement in sustainability. Can you expound on that?
Are our clients maximizing the water recovery rates and minimizing the energy consumption of their plants? We want to extend the life of disposable membranes and reduce chemical consumption used in cleanings. The overall water recovery and hence the amount of water rejected to waste in the purification process can be a function of a number of factors, including raw water quality, the degradation or fouling of membranes and resins, mechanical problems or other issues. Data analytics can be used to maximize water recovery where it might otherwise go unnoticed and hence, decrease a facility’s water footprint. Energy and maintenance savings can be had not only through increases in water recovery, but also by extending operation and reducing the number of starts and stops. If we can improve operations so that we consume less filters and membranes, that means less waste to the environment. The same can be said of chemical consumption, whether they are used in normal operation or maintenance cleanings. I think a sharing of best practices and information based upon hard data can have a significant impact on sustainability initiatives. From an environmental standpoint, a water plant has a relatively significant impact compared to many other industrial processes.
Finally, can you share your view of big data as it relates to water purification in the future?
Retail vendors and credit card companies know my spending habits and use that data not only to sell me things I might be interested in but also to protect me from theft and fraud. The technology is here, and it will have a significant impact on the water industry. Ideally, we will see data analytics impact the larger water issues of scarcity, contamination and sustainability.