Case Study: Water Cooling Systems for Pharmaceutical Manufacturing
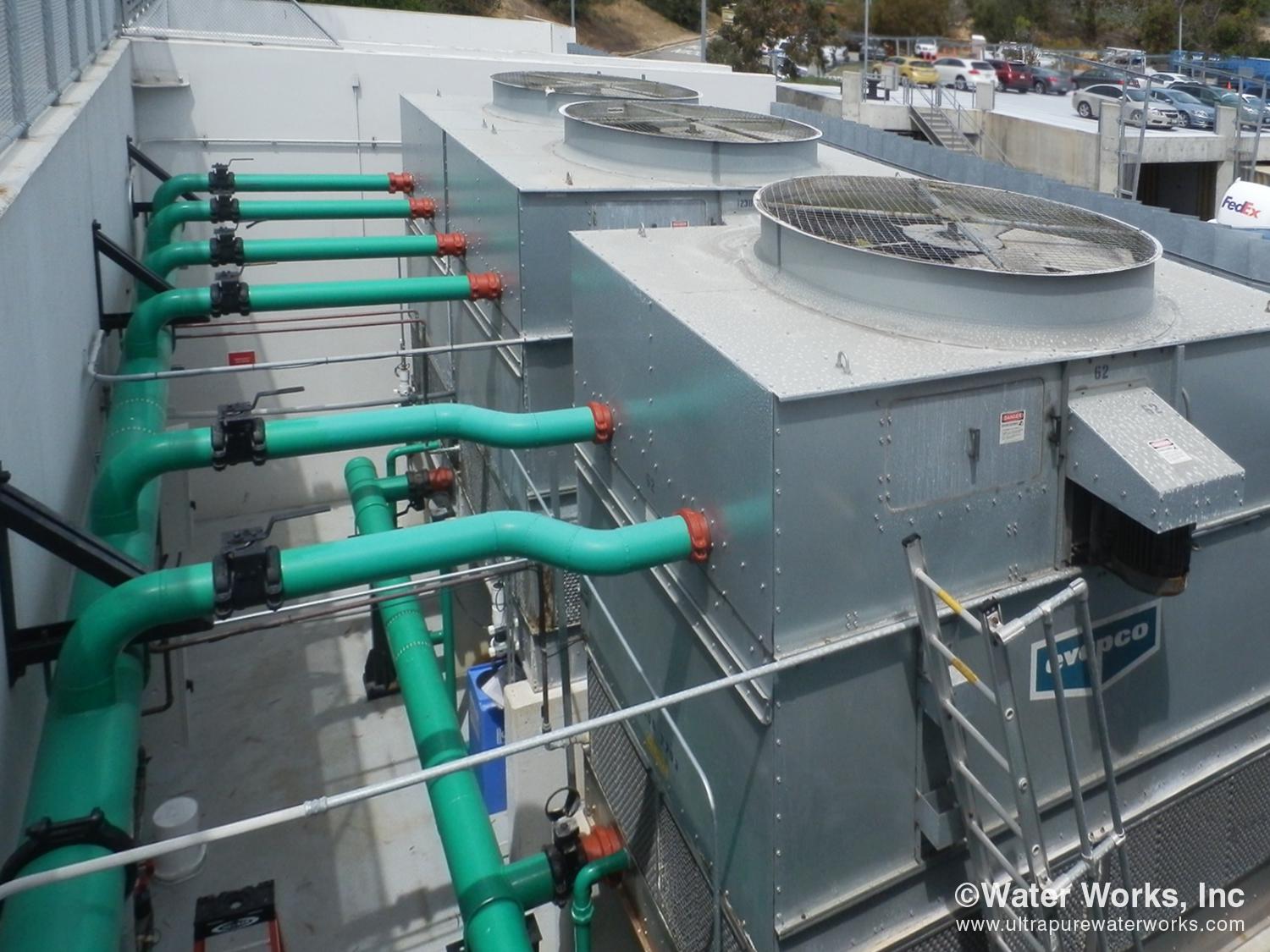
Thermal management is essential in pharmaceutical manufacturing, where many production processes generate substantial heat. Efficient, reliable cooling systems not only support product quality and safety but also contribute to operational uptime and energy efficiency.
In today’s regulatory and environmental landscape, pharmaceutical manufacturers increasingly prioritize sustainable cooling solutions that minimize water consumption and lower energy costs—all while maintaining cGMP compliance.
Smart Cooling for a cGMP Acute Care Manufacturer – San Diego, CA
MECO’s San Diego-based team (formerly Water Works, Inc.) partnered with a specialty pharmaceutical company to deliver a custom-engineered water-saving cooling system for its cGMP manufacturing facility. The company focuses on commercial and clinical development of acute care products and required a solution that would reduce water use while scaling with production growth.
Project Overview
The customer’s original EDI system was replaced with a more robust deionization (DI) skid and a redesigned cooling infrastructure to support rising operational demands.
One of the key innovations involved the reuse of reverse osmosis (RO) concentrate as makeup water for the facility’s cooling towers—dramatically reducing freshwater consumption. By increasing conductivity blowdown cycles from 3,500 to 10,000 micromho, the facility achieved significant conservation gains.
Measurable Impact
The RO concentrate reuse system—applied during the chilling phase of manufacturing—helped cut annual water consumption by an estimated 4–5 million gallons.
Preliminary data from water meters over a four-month span reported:
- 575,700 gallons of RO concentrate used
- 211,000 gallons of soft water used
This data underscores the dramatic shift toward sustainable, water-wise operations.
Smart System Design for Sustainable Cooling
The cooling system supports three 180-ton chillers, with two typically operating and the third held in reserve for seasonal peaks. To optimize water use, MECO implemented a dynamically controlled water selection system:
- Automated monitoring selects the water source based on cooling tower levels
- RO concentrate is prioritized when available
- Soft water acts as a supplemental source during high-demand periods
- Solenoid valves and level controllers ensure safe, efficient water distribution
This adaptive design ensures the system remains responsive while minimizing freshwater dependency—a key advantage in drought-prone regions like California.
We Bring the Ultrapure Water. You Bring the Breakthroughs.
MECO’s cooling and water purification systems are engineered to maximize performance, sustainability, and compliance. Whether for purified water, RO reuse, or cooling system integration, we help pharmaceutical manufacturers operate smarter, conserve resources, and stay audit-ready.
Contact MECO to explore how our water solutions can support your next breakthrough.