WFI Risk, Reliability, and Sustainability
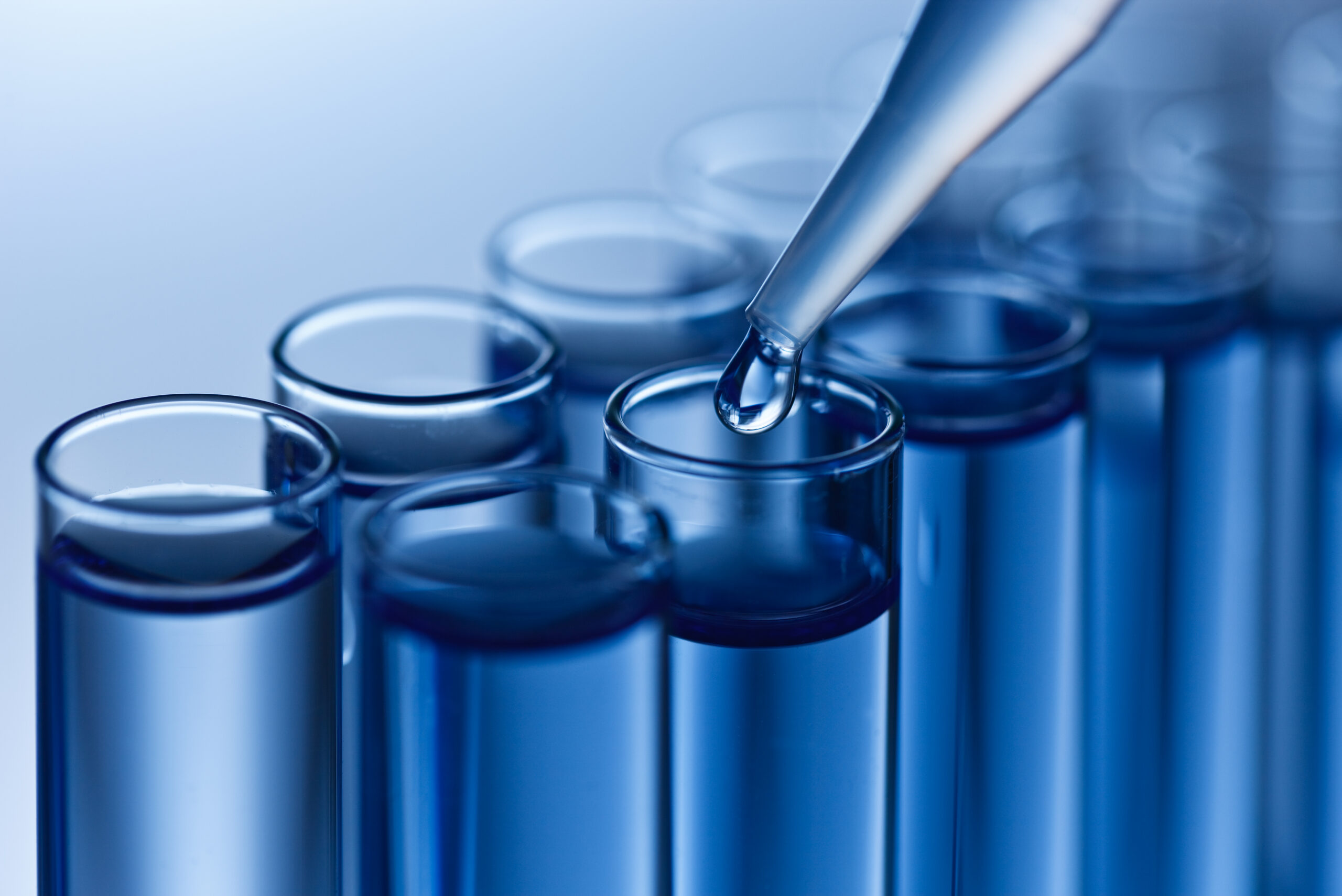
CRITICAL FACTORS WFI PRODUCERS SHOULD CONSIDER WHEN CHOOSING GENERATION SYSTEMS
Written by: Mike Wojcik, Director of MECO North American Sales; Bill Essary, MECO Service Manager; Ian Shanahan, European Business Development Manager at Flow Technology Ltd.
As a manufacturer of pharmaceutical or biologic medicines, you want to evaluate all of the issues surrounding your design choice for critical water production. Membrane-based production of Water for Injection (WFI) continues to be at the forefront of discussions and does present a design alternative. As you may know, while the US Pharmacopeia has long allowed WFI production by distillation or means proven to be equal or superior, the European Pharmacopeia revised its monograph to be similar in 2016. Specifically, the EU Pharmacopeia allows the use of “a purification process equivalent to distillation such as reverse osmosis (RO) coupled with appropriate techniques.” In addition to harmonization, some additional goals of the change are to lower cost and provide a more sustainable approach to water production. Cost is an important consideration in the design criteria of any water production system. For a more in-depth discussion of cost, “A Cost Review of Alternative Systems for Producing Water for Injection (WFI), Including Membrane-Based WFI Production Absent Distillation” is available to you at https://www.meco.com/cost-review-of-wfi-systems. But, as owners and engineers make design decisions, risk, reliability, and sustainability are also important topics. This piece highlights these three additional considerations regarding the pros and cons of alternative methods of WFI production. It is important to note that the choice of generation system (distillation or membrane-based) impacts the storage and distribution system, particularly the control and prevention of microbial contamination. Since there may be different risk, reliability, and sustainability issues related to storage and distribution, we did not include them in this piece.
Download a Copy of the WFI Risk, Reliability and Sustainability Paper
Risk
Water for Injection (WFI) is one of the most critical ingredients in the pharmaceutical manufacturing process. Minimizing the risk to the quality of water produced is important when designing, building, operating, and maintaining a given water system. When evaluating a new WFI system, you will want to determine the potential risks, their associated consequences, frequency of occurrence, detectability, and corrective actions required.
When the European Pharmacopoeia monograph <0169> was revised in 2016 to include WFI by non-distillation membrane-based systems, the European Medicines Agency (EMA) published a Q & A paper with their main concern being microbiological proliferation and the associated by-products (exotoxins and endotoxins). The inside of a membrane-based system is not of sanitary construction, is an ideal environment for and readily promotes biological activity. In addition, the raw water is at a significantly higher pressure than the product side of each unit operation. As such, the EMA concerns are warranted. Each unit operation (reverse osmosis, electrodeionization, and ultrafiltration) provides a unique function and is critical to the maintenance of water quality. In addition, the quality of the individual component manufacturers is also very important. If contamination from one unit operation to the next were to occur, will it be adequately detected?
In order to eliminate biofilms, membrane-based systems are heat and chemically sanitized. Periodic cleanings are also important as well since
organic matter becomes a food source for bacteria, exacerbating the biofilm growth. A robust preventive maintenance (PM) schedule is a must. With the help of your equipment supplier during qualification, you will determine how often the system will be down for PM activities. Membrane-based WFI systems could be down multiple times a year for elastomer replacements, resin/carbon change-outs, cleanings, and component replacements. Every time the system is opened, there is exposure to contamination and the possibility of incorrect installation of these key components. If you have a third party perform this work, they should be well vetted.
Reliability
Water systems operating at 65 – 80C are recognized as self-sanitizing. Membrane systems operating at ambient temperatures require a robust preventive maintenance protocol that will ensure the water system produces expected compendial quality continuously and reliably.
Any WFI system is composed of multiple unit operations to achieve the final water quality required. Systems with fewer unit operations tend to be more reliable as there are fewer things that can go wrong. The reliability of any system is less than the lowest reliability of any of its unit operations. Typical WFI systems include the following: VC Distillation — Softeners, Carbon Filter, and the VC Still. Membrane-based WFI generation — Softeners, Carbon Filter, RO (single or two-pass), Electrodeionization, Ultrafiltration, and a means of periodic chemical and/or heat sanitization.
A membrane-based water system’s performance is directly linked to the feed water quality. As such, they have to be designed and operated to handle the extremes of feed water quality that can differ seasonally. Frequent sampling and monitoring of the feed water and points within the water system are critical. Daily sampling is required at each step of the purification process and every use point during the validation process. At a minimum, the system should include conductivity, temperature, pressure, and flow monitors. Action limits of <10 Colony-Forming Units (CFU)/100ml for WFI should be used while finalizing Standard Operating Procedures (SOPs). Once SOPs are finalized, qualification is completed after daily routine sampling at a single point of use and weekly for all other Point of Uses (POUs) for an entire year. Sampling/monitoring for endotoxin is also required. This data is paramount to support the SOPs.
Biofilm will form and can slough off, making microbial counts vary greatly. A continuous flowing system will reduce the formation of biofilm. A robust preventive maintenance program is required that typically includes chemical sanitizations at least annually and heat sanitizations weekly to biweekly. Frequent sanitizations or need for cleaning/ defouling due to poor operation and maintenance in upstream pretreatment equipment will lead to performance issues and a shortened lifespan, requiring costly replacements. Installing a robust process monitoring system, like MECO smartANALYTICS, can help mitigate reliability issues through real-time trend analyses and up-to-date reporting on system health, resulting in proactively planned routine maintenance.
For membrane-based systems, it is important to remove organics (food source for bacteria) from the system, so Total Organic Carbon (TOC) monitors have been recommended at multiple points in the generation system. Online Active Fluorescent Units (AFU) bioburden/microbial analyzers have been recommended to be installed throughout the system as well. However, there are still concerns with these instruments regarding validation and the correlation of AFU to CFU. All of these instruments must be calibrated on a regular basis. Adequate time must be budgeted for the proper maintenance of the system.
View Our Pharmaceutical Solutions
Some other maintenance items to be considered in order to ensure a reliable system are:
- Replace elastomers annually.
- Replace carbon every year. (Some feed waters may require more frequent replacements). Chemically sanitize vessel after carbon removal.
- Sample and test softener resin annually and replace every 1 to 3 years.
- Chemically clean RO membranes every 3 to 6 months. Replace with new membrane every 18 to 24 months.
- Replace or refurbish CEDI modules every 3 years or after 80 to 90 heat sanitization cycles.
- Replace UF modules as required. Test for integrity annually.
- Replace UV lamps, quartz sleeves, and related elastomers every 6 to 12 months.
- Alarm testing and instrumentation performance should be verified every 6 months and re-calibrated annually.
A maintenance contract with the system supplier is important and will help keep the system operating reliably.
Sustainability
Aside from differences in risk and reliability, today’s choices of WFI generation technology also pose questions about how sustainable those processes are long-term. Sustainability focuses on meeting the needs of the present without compromising on the ability of future generations to meet their needs. We can think of sustainability as three pillars: Economic, Environmental, and Social. More colloquially we could say: Profits, Planet, and People.
Profits
The direct cost of inputs to a WFI system will play a part in a site’s overall operating costs. Sourcing inputs (electricity, steam, chemicals, chilled water) from unsustainable sources will incrementally affect profits as costs increase. This is very true of fossil fuel sources of electricity and steam, as more governments globally are increasing carbon taxes on fossil fuels in an effort to incentivise more sustainable energy sources, particularly in the EU. The vast majority of industrial steam is generated from systems using fossil fuels. A WFI generation system that reduces its need for large amounts of high-pressure steam may be more sustainable going forward, especially companies that have a cogeneration plant. Vapor compression distillation and membrane WFI systems use lesser amounts of steam than a multiple effect distillation system (VC uses less, sometimes using electric boilers, while an ozonated membrane system may use no steam at all).
The costs of renewable electricity sources continue to drop globally, and a WFI system designed to use more of these sources can realize future cost savings as the cost per kWh of this electricity on the grid continues to fall. Experts expect this trend of renewables becoming cheaper than fossil fuels to continue, especially as more large grid energy storage systems are constructed (hydropower, rail energy storage, compressed air storage, hydrogen storage, etc.). As this brings down the overall wholesale electricity costs on a given grid, it benefits systems that are more electrically powered than steam powered, protecting a site from volatile and rising utility costs.
Planet
The most pertinent consideration in the sustainability of a WFI Generation system is its carbon footprint and environmental footprint. Biomass boilers for steam from sustainably managed forests can be carbon-neutral (i.e., they only release as much carbon as absorbed in their lifespan, meaning a net zero gain in atmospheric carbon), while a fossil fuel will be carbon positive, and contributing to man-made climate change via the “greenhouse effect.” If a site has an available and sustainable source of low-to-zero carbon energy sources, then utilizing that will greatly influence the sustainability of their site.
The question of waste is also a factor in the sustainability of a WFI system from an environmental point of view. Distillation systems are made primarily of stainless steel, which does require large amounts of energy to produce but is often considered as more of a “green” material, as it can be completely recycled, and its environmental credentials grow with each use and reuse. Reverse osmosis systems require consumable membranes, which require cleaning and eventual replacement. Unless the membranes can be cleaned and reused in other applications, the only option for dealing with end-of-life membranes is disposal to landfill. Considerations must also be given to the impact of the chemicals required for cleaning of Membrane WFI systems. If not treated correctly, they can cause environmental harm when discharged to waste.
People
Aside from the topics already discussed, we should consider how staffing for the varying WFI generation systems could ensure a more sustainable planet for future generations. Membrane WFI systems will undoubtedly require more physical attention from operators on site, as they will require cleanings, membrane change-outs, and frequent sampling to ensure consistent product quality. As pointed out in the “Risk” section, while a distillation system typically requires maintenance once annually during shutdown, a membrane WFI system may require multiple shutdowns per year. It is becoming more difficult for sites to hire and retain trained staff with the correct knowledge base and experience to operate and maintain these “hands-on” WFI generation systems. While distillation systems tend to be more “hands-off,” they offer a more sustainable staffing solution.
View Our Pharmaceutical Solutions
Summary
The harmonization of standards has opened more options to WFI manufacturers in the biopharmaceutical industry, and a careful analysis of key factors in decision-making reveals the pros and cons associated with membrane-based WFI systems.
While a membrane-based system offers capital advantages, the OPEX to maintain a system free from biofouling takes a toll on those gains. What should be carefully considered is the need for continuous sanitization, routine maintenance and cleaning of the system. A robust maintenance contract plan with your system supplier is critical to keep your system operating reliably. With the appropriate frequency of sampling, on-site expertise can reduce the risk of contamination of the system. Overall, membrane-based WFI systems appear to be a more complicated solution for WFI manufacturers, but with the proper system supplier, you can minimize risk, increase reliability, and achieve long-term sustainability.