Purified Water Systems for Pharmaceuticals
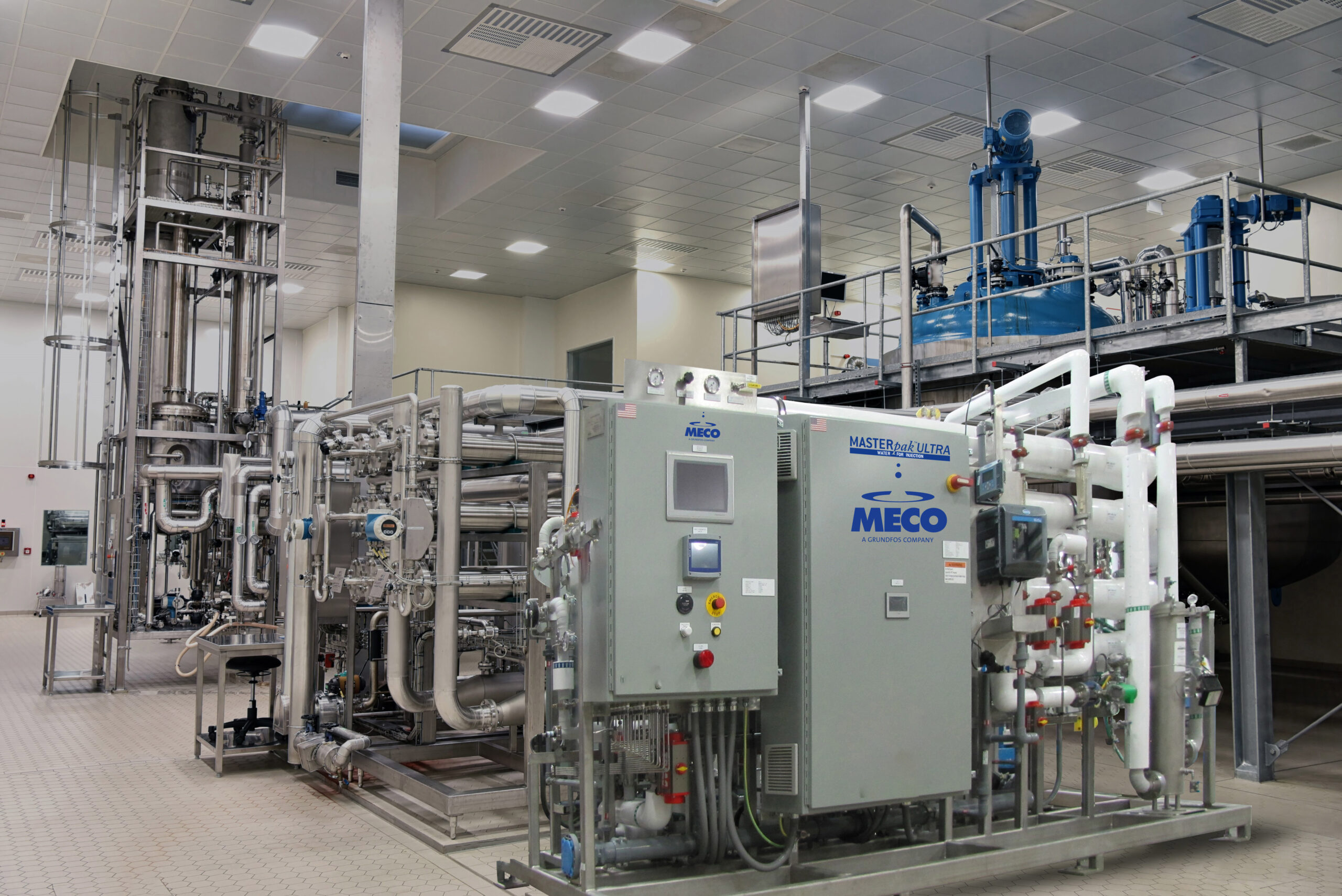
The pharmaceutical industry utilizes purified water as one of the main ingredients for processing, formulating, and manufacturing pharmaceuticals and other active ingredients. Water can be used to reconstitute products, aid in synthesis, as a cleaning agent, and for the production of finished products. The USP monographs explain the various water grades used for pharmaceutical production and acceptable methods to produce each. In general, water can be separated into two types: bulk waters and packaged waters. Bulk waters are commonly produced on the site where they will be used. Packaged waters are produced, packaged, and sterilized to prolong product shelf life and preserve their microbial qualities. Depending on the specific pharmaceutical use case, different water grades are required.
What Is Purified Water for Pharmaceuticals?
Purified Water is a grade of pharmaceutical water used as an excipient in the production of non-parenteral preparation for pharmacology including tests and analyses.
Purified Water Methods Used in the Pharmaceutical Industry
Purified pharmaceutical water systems typically include two stages that treat the facility’s feed water, which must always meet the local regulatory requirements for potable water quality. Pretreatment is the initial stage, which modifies the water quality to reduce target contaminant groups that can damage or otherwise interfere with the performance of downstream unit treatment processes. At a minimum, these contaminant groups typically include suspended solids, hardness, and other scale forming minerals, and disinfectants such as chlorine and chloramine. Some systems include more advanced pretreatment to address other contaminants such as biological and organic foulants, and overall total dissolved solids (TDS).
The second stage is the final treatment, sometimes called preparation, which further treats the pretreated water to meet the final purified water quality requirements. Most modern systems include at least one pass of reverse osmosis to reduce all contaminant groups except gasses (e.g. inorganic, organic, and biological) followed by a polishing step, such as Electrodeionization (EDI) or other deionization processes, to further reduce conductivity below the target limit before storage. Additional post-treatment technologies can also be included depending on the requirements of each individual application, such as UV, submicron filtration, and ultrafiltration.
MECO MASTERpak™ Purified Water Product Line
Since their inception in 2004, MECO’s MASTERpak™ systems are based on a proven hot water sanitizable system design with a robust feature set and proven performance to assure reliable ambient generation of both purified water and Water for Injection that meets or exceeds the requirements of the major global pharmacopeia (USP, Ph. Eur., and JP). The hot water sanitization capabilities assure superior performance for microbial purity, and the systems are highly configurable to meet the unique needs of each individual project. The MASTERpak™ and MASTERpak™ ULTRA systems offer a wide range of configurations including 1- or 2-pass reverse osmosis, 6000 MWCO ultrafiltration, UV, and other features commonly requested in Purified Water system design.
Partner with MECO for Purified Water Systems
Pharmaceutical-grade Purified Water can be achieved through various methods to reach the required levels based on pharmacopeia requirements. MECO offers the broadest base of solutions for purified water in the industry. With over 90 years experience in the business, our team can support you every step of the way from design, installation, and service. To learn more about how MECO’s Purified Water solutions, contact our MECO team.