What You Need to Know Before Buying a Membrane-Based WFI System
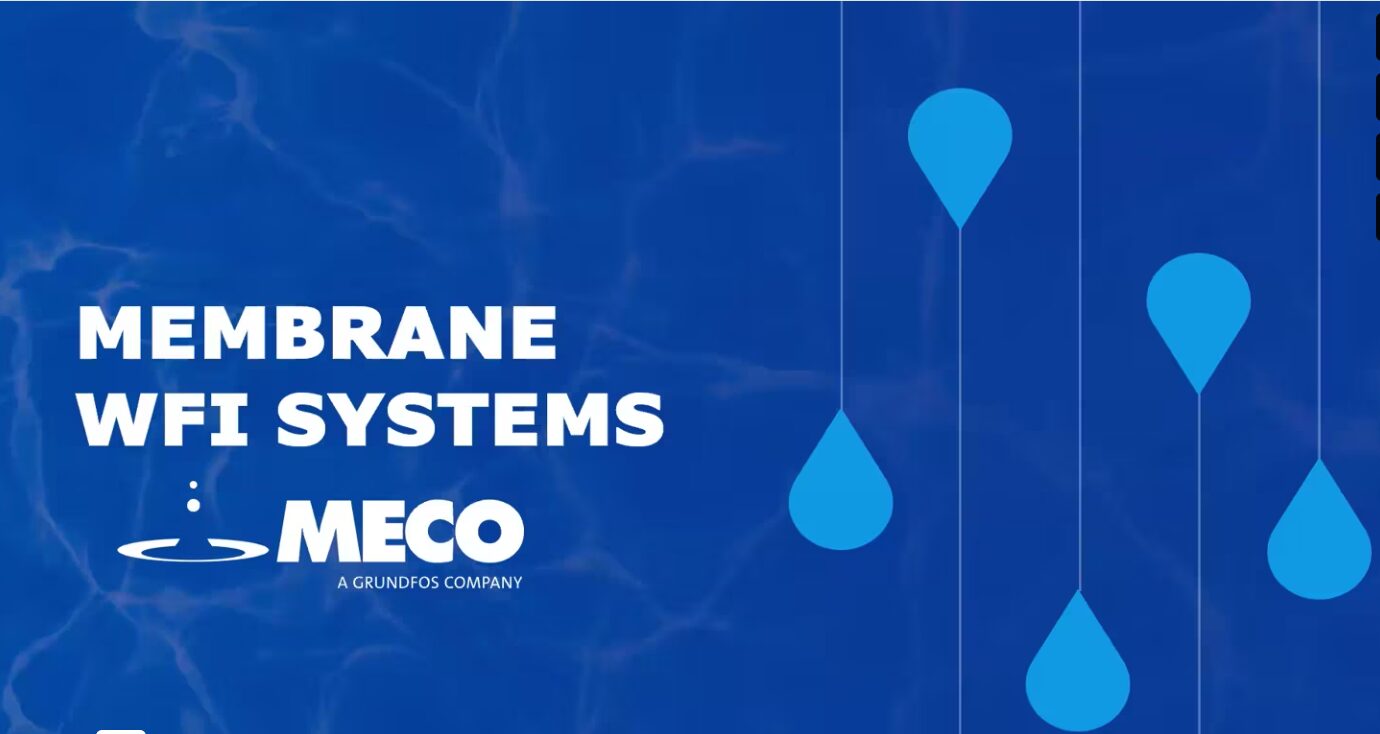
Water for Injection (WFI) is a critical utility with increasing demand for vaccines and therapeutics. Traditionally, WFI production uses distillation, but producers that use such systems want options with lower ownership costs and more sustainability. Reverse osmosis (RO) membrane-based systems with ultrafiltration can meet some of these challenges.
If you are a manufacturer of pharmaceutical or biologic medicines, you’ll want to evaluate all the pros and cons surrounding your design choice for a new WFI generation system.
Membrane-based production for WFI continues to be at the forefront of discussions as it presents a design alternative to the traditional distillation-based system. Membrane-based production of WFI has the potential to lower total cost of ownership and possibly provide a more sustainable solution long-term.
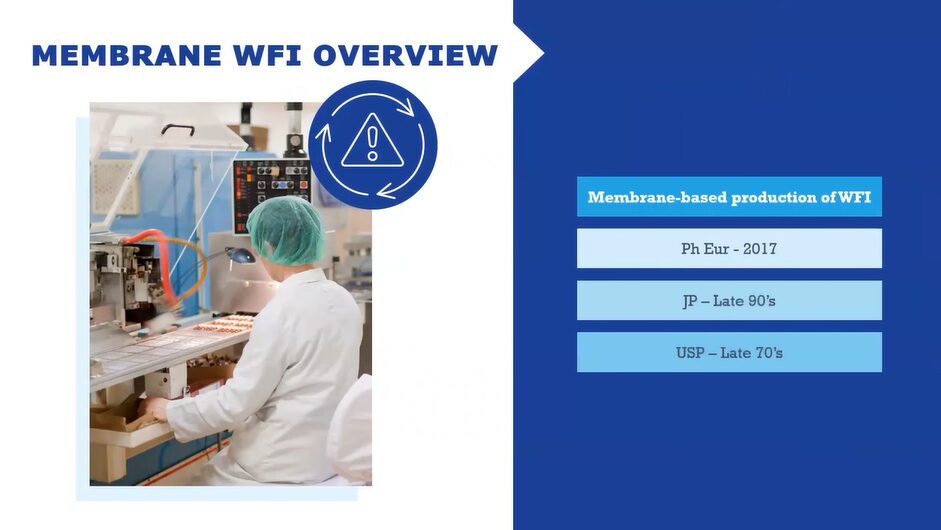
Regulatory and Quality Requirements for WFI
Producers implementing membrane-based WFI systems must first consider regulatory and quality requirements, including those from the United States Pharmacopeia (USP), European Pharmacopeia (EP), and Japanese Pharmacopeia (JP).
Each set of regulatory standards differs slightly in the allowed WFI production processes. The standards require purification processes equivalent or superior to distillation, with some unique requirements, like no added substances. These equivalent systems can include membrane-based purification.
USP Monograph outlines WFI must be purified by distillation or a purification process that is equivalent or superior to distillation and that it contains no added substances.
The European Pharmacopeia (Ph. Eur. Monograph 169) outlines a purification process that is equivalent to distillation. Reverse osmosis, which may be single-pass or double-pass, depending on water coming into your facility and other risk-based questions, coupled with other appropriate techniques such as electrodeionization, ultrafiltration or nanofiltration, is suitable. Notice should be given to the supervisory authority before implementation.
Japanese Pharmacopeia requires WFI by distillation or reverse osmosis and/or ultrafiltration. It’s important to know that the JP requires the molecular weight cut-off of your final membrane barrier to be at 6,000 Dalton.
The regulatory standards also set slightly different benchmarks for conductivity, total organic carbon, bacterial, and microbial levels.
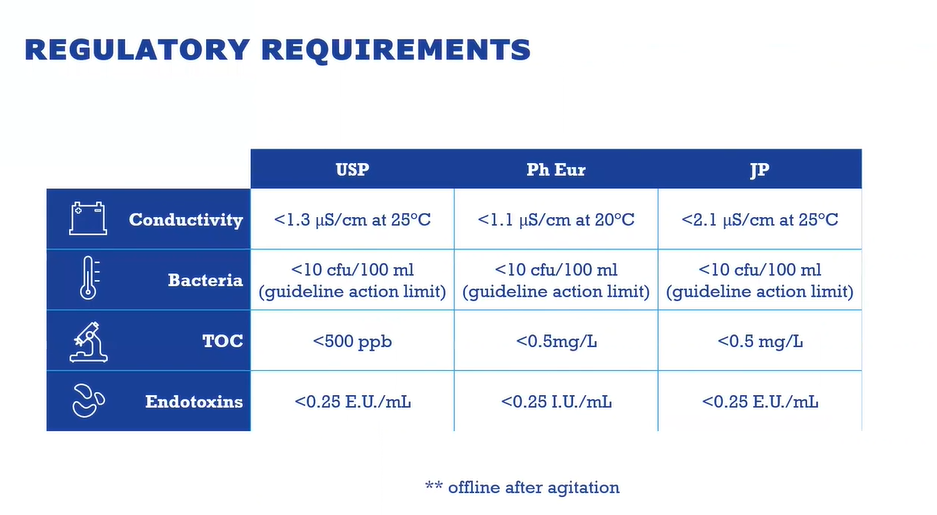
Learn more about navigating global pharmacopeia standards for water quality here.
Operations of a Typical Membrane WFI System
Membrane-based WFI systems meet regulatory standards through comprehensive system design, including the following components:
- Pretreatment: The first subsystem that would see water is the pretreatment, which protects the final treatment (generation) from damage. It conditions the water so it is acceptable for feeding into the final treatment or generation subsystem.
- Final treatment: This component forms the heart of the system that produces the final required quality and quantity of Water for Injection (WFI). The membrane gets implemented here.
- Storage and distribution: After proper purification, storage and distribution systems ensure adequate water volumes with sufficient pressurization for point-of-use requirements.
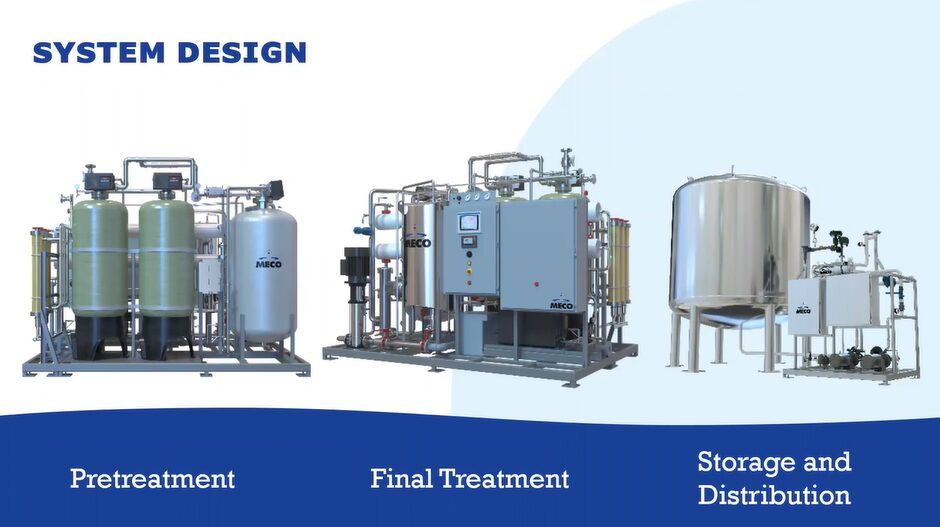
Before you implement a membrane-based system, there are four main areas to evaluate before designing your system. For example purposes, we’ll be using Water for Injection (WFI) to explain the importance of each.
- Feed water quality and temperature: What’s your starting water quality? There are a number of different contaminant groups to evaluate to make sure each can be adequately treated to guarantee Water for Injection quality at the outlet of the system. This usually comes from a standard laboratory water analysis of whatever the local feed water source. The other area to consider is temperature and any seasonal variation of that temperature, which is a particular concern with surface water and parts of the world that have large temperature swings between seasons. This is important because membrane-based systems’ performance is affected by the feed water temperature.
- Peak water usage: This will directly impact the storage tank size and also will inform what the flow rate will need to be.
- Daily water usage: The total amount of water that will be used on any given day. You will also want to know worse-case scenario. This impacts the final treatment or generation system as it will have to make enough water safely to satisfy that total daily demand.
- Point of use temperature required: There are some applications that use ambient water and others that require hot. MECO has designed a number a systems that have different temperature requirements at different points of use. This can all be accounted for in the storage and distribution design of a membrane-based Water for Injection system.
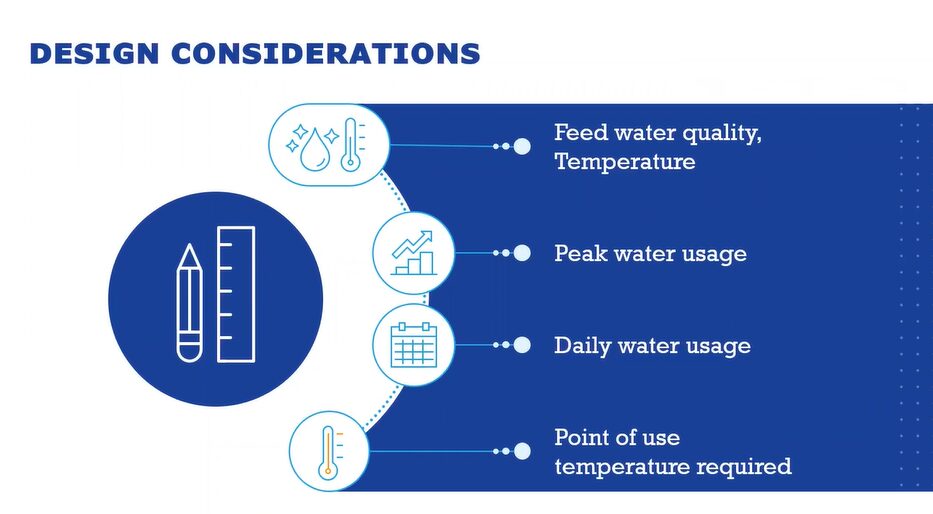
Contaminants in Water
There are a number of contaminant groups that need to be considered when designing your membrane-based system. The purpose of pretreatment is to condition the water before it is fed to the generation system. The typical three groups of contaminants are particulates (suspended solids), scalants/foulants (calcium/magnesium) and disinfectants (C12).
Our Membrane WFI System cannot tolerate high levels of particulates. Particulates can be removed through a variety of options in our pretreatment subsystem, such as bag filter cartridge or multimedia filter.
Scalants and foulants have to be removed or reduced during pretreatment as they produce chemical compounds that interfere with the membrane’s performance. This jeopardizes the output quality and quantity of the system.
Lastly, disinfectants must be removed. Disinfectants are added to public water to protect the public health but those disinfectants are damaging to the membrane by causing oxidative damages to membranes and EDI stacks.
Unit Processes in Membrane Based WFI System
In our pretreatment subsystem for membrane-based water purification systems we remove particulates through a multimedia filter composed of anthracite, sand, fine garnet, course garnet, medium or course gravel. The typical removal rate is about 10 microns, which is industry standard for media filters.
For companies who want to cut down their water footprint, we can use pleated dev filter or bag filter for the pretreatment subsystem. The downside to these filters are they have higher maintenance as someone will consistently need to change the filters.
The filtrate will exit that vessel and move on to the next step of water softening. We use a resin bed in order to remove the calcium and magnesium from the feed water. The hardness must be removed so it does not scale the membranes. This will release sodium, since we are using salt to regenerate that bed.
Chlorine is then removed from the feedwater using activated carbon. Our membranes have about 1000 PPM hours of chlorine tolerance so you can run at 1PPM of chlorine for 1000 hours before you see damage to the membrane. The EDI stacks generally cannot handle chlorine, which is why this stage of chlorine removal from feedwater is so important.
Carbon filters are tried and true when it comes to removing chlorine. Chemical injections can be tricky to manage, for example you don’t have a good injection rate, your pump isn’t putting out what it needs or a bad batch got mixed up. Chemical injections are just not as reliable in removing chlorine as carbon filters. For UV chlorine removal, it is hard to get 100% kill of the chlorine guaranteed.
Dechlorinated water will then exit the carbon filter and proceed to final treatment.
First step is the RO, which will reduce the bulk of all contaminant groups (single or double pass depending on water quality). Next step is EDI stack, which uses a mix of electricity, membranes and resin in order to polish what comes out of the RO. This further reduces inorganics and some organics. The final barrier is the UF, which is where the 6000 Dalton membrane will be used in order to reduce biological contaminants.
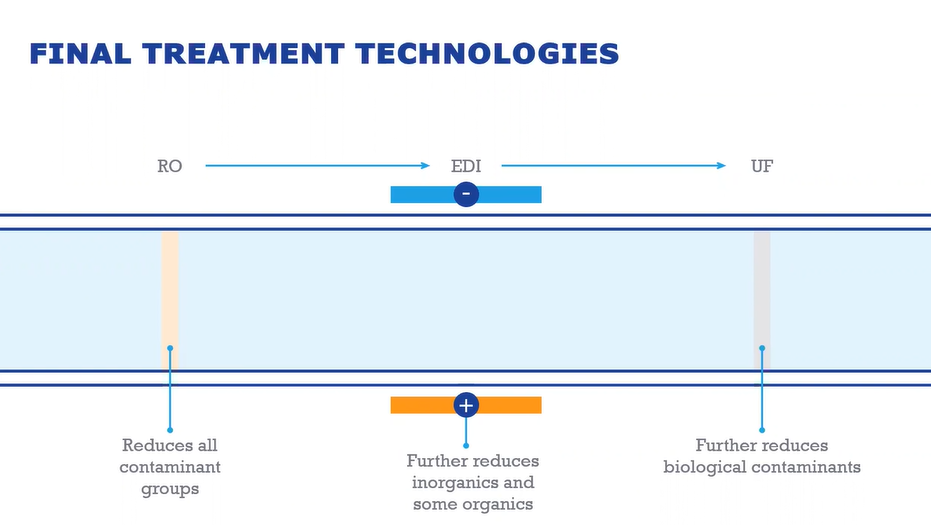
After this step the system sends the water to a storage tank.
Learn more about the cost differences between the four main system designs for Water for Injection here.
There are three types of sanitation methods for storage and distribution:
- Thermal (most popular method)
- Ozonation
- Chemical (difficult to deal with, time consuming and hard to rinse out)
Risks of a Membrane-Based WFI System
Water for Injection (WFI) is one of the most critical pharmaceutical manufacturing ingredients and therefore extra precaution must be taken in identifying and preventing risks. Controlling risks involves:
- Identifying risks
- Considering their consequences
- Determining how often the risk could occur
- Setting up systems to detect risks
- Deciding how to take corrective action
Membranes can grow bacteria at any point in the system and the best way to deal with that is hot water sanitization. This is the most popular way to reduce risk of contamination of your membrane-based water purification system.
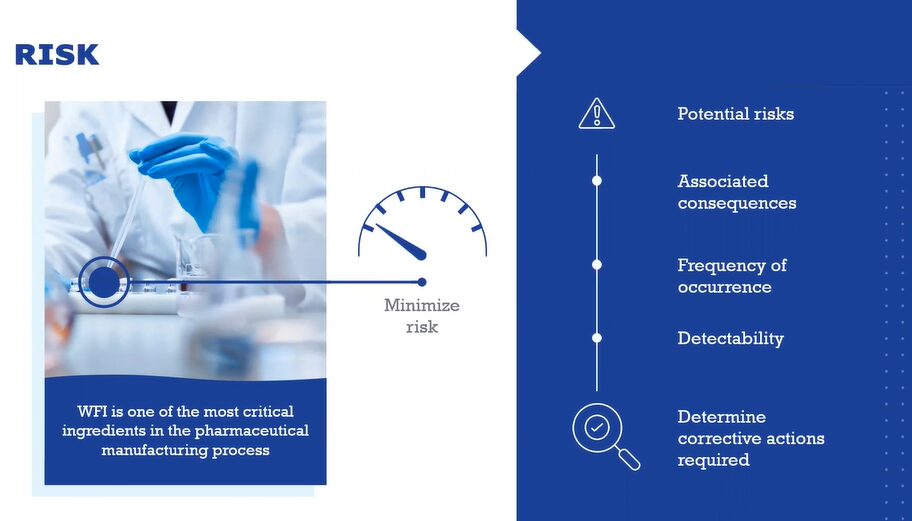
Since membrane systems operate at ambient temperatures, they require robust predictive maintenance, and their complexity can also influence reliability. In distillation water purification systems, you’re operating at self-sanitizing temperatures (65-80C).
It’s important to have a preventative maintenance (PM) protocol set up for any membrane-based WFI system as well.
Read more about WFI risk, reliability, and sustainability from our whitepaper here.
The MECO Membrane WFI System
The compact MASTERpak™ULTRA provides a complete solution for producing ambient WFI using membranes. The unit incorporates MECO’s pretreatment, RO, electrodeionization and ultrafiltration capabilities. Get in touch today to see how MECO can help with a membrane-based WFI system.
Water our full webinar on Membrane WFI Systems below.